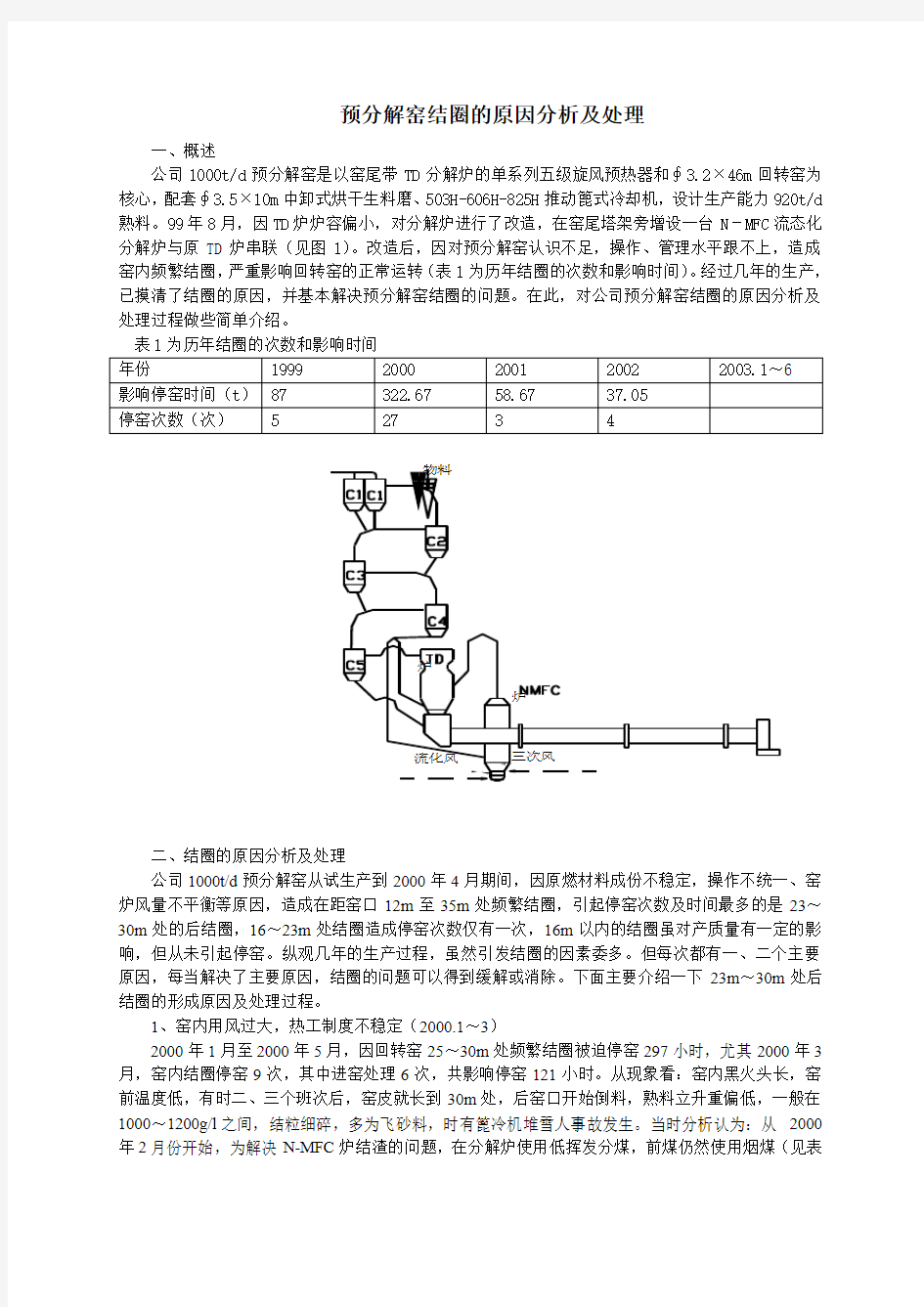
预分解窑结圈的原因分析及处理
- 格式:doc
- 大小:61.00 KB
- 文档页数:3
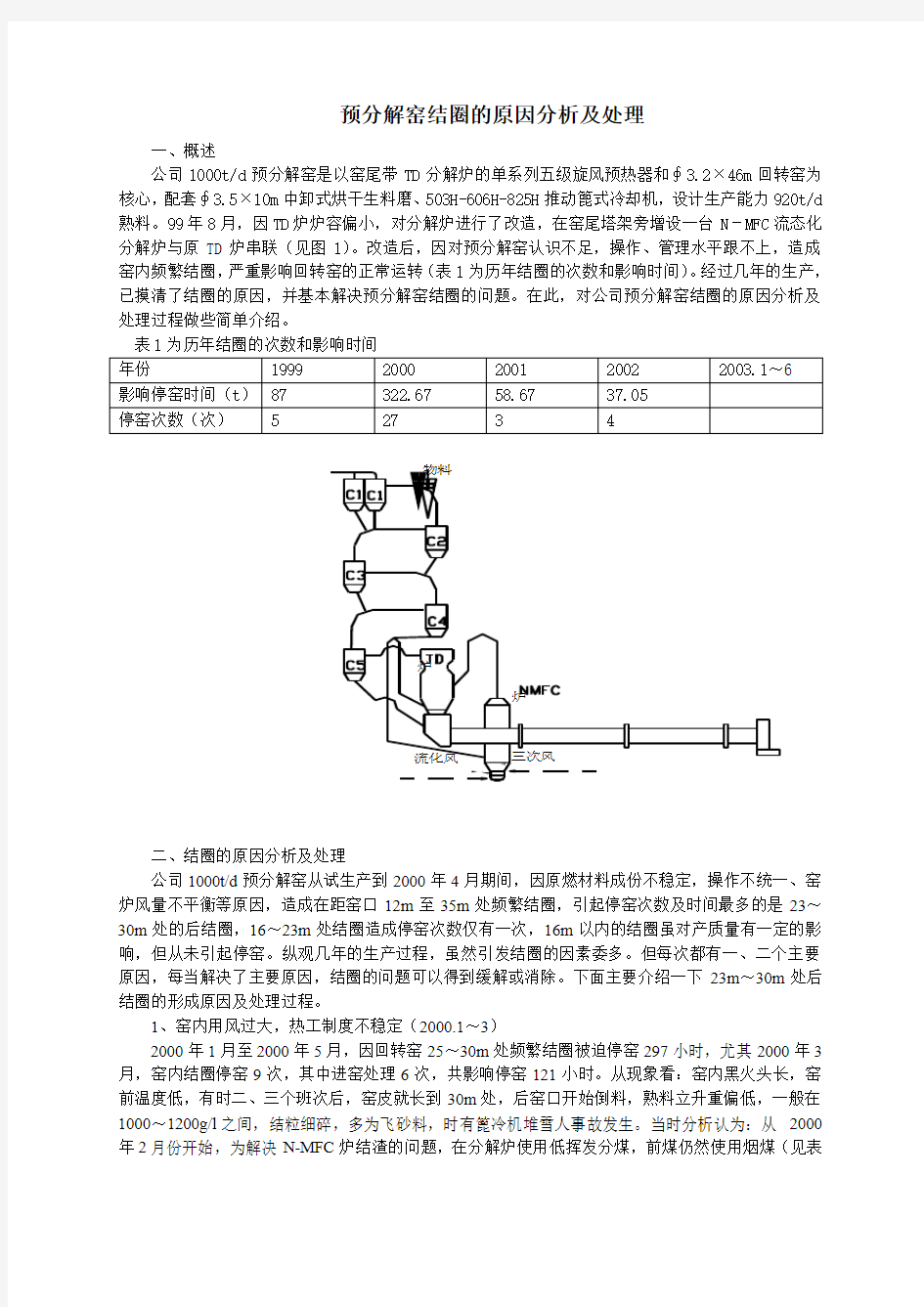
预分解窑结圈的原因分析及处理
一、概述
公司1000t/d预分解窑是以窑尾带TD分解炉的单系列五级旋风预热器和∮3.2×46m回转窑为核心,配套∮3.5×10m中卸式烘干生料磨、503H-606H-825H推动篦式冷却机,设计生产能力920t/d 熟料。99年8月,因TD炉炉容偏小,对分解炉进行了改造,在窑尾塔架旁增设一台N-MFC流态化分解炉与原TD炉串联(见图1)。改造后,因对预分解窑认识不足,操作、管理水平跟不上,造成窑内频繁结圈,严重影响回转窑的正常运转(表1为历年结圈的次数和影响时间)。经过几年的生产,已摸清了结圈的原因,并基本解决预分解窑结圈的问题。在此,对公司预分解窑结圈的原因分析及处理过程做些简单介绍。
二、结圈的原因分析及处理
公司1000t/d预分解窑从试生产到2000年4月期间,因原燃材料成份不稳定,操作不统一、窑炉风量不平衡等原因,造成在距窑口12m至35m处频繁结圈,引起停窑次数及时间最多的是23~30m处的后结圈,16~23m处结圈造成停窑次数仅有一次,16m以内的结圈虽对产质量有一定的影响,但从未引起停窑。纵观几年的生产过程,虽然引发结圈的因素委多。但每次都有一、二个主要原因,每当解决了主要原因,结圈的问题可以得到缓解或消除。下面主要介绍一下23m~30m处后结圈的形成原因及处理过程。
1、窑内用风过大,热工制度不稳定(2000.1~3)
2000年1月至2000年5月,因回转窑25~30m处频繁结圈被迫停窑297小时,尤其2000年3月,窑内结圈停窑9次,其中进窑处理6次,共影响停窑121小时。从现象看:窑内黑火头长,窑前温度低,有时二、三个班次后,窑皮就长到30m处,后窑口开始倒料,熟料立升重偏低,一般在1000~1200g/l之间,结粒细碎,多为飞砂料,时有篦冷机堆雪人事故发生。当时分析认为:从2000年2月份开始,为解决N-MFC炉结渣的问题,在分解炉使用低挥发分煤,前煤仍然使用烟煤(见表
2),在使用过程中有混用的现象。因烟煤煤质差、波动大,加上低挥发分煤的混入,煤质波动更大,造成窑内火焰忽长忽短,煤灰掺入量时多时少,物料成份波动大,窑热工制度不稳定,是结圈的主要原因。通过加强原煤进厂和煤粉制备过程中的管理,减少前后煤的混用,提高了煤质的稳定性,结圈事故虽有所缓解,但未能从根本上解决结圈的问题。后来,在处理结圈的过程中发现:在物料及煤粉全部入TD分解炉,N-MFC炉内不分料的情况下,窑运行三、四个班次后,窑内结圈基本可以消除,主窑皮恢复到13~14米。由表1可见,当N-MFC炉切换到TD炉煅烧时,在喂料量、高温风机转速不变的情况下,烟室负压下降,三次风压上升,TD炉入口、高温风机前负压下降。说明窑内通风减少,炉列通风增加,系统阻力减少,总风量增加。从以上参数的变化及公司TD分解炉的性能来看,采用TD炉煅烧处理结圈时,工艺方面主要发生以下变化:1)物料及煤粉全入TD炉时,MFC炉仅充当三次风管的作用,阻力损失减少,炉列通风量增加,窑内通风减少,烧成带风速减慢,火焰相对集中,高温带前移;2)TD炉炉容小,物料及煤粉在炉内停留时间短,入窑物料分解率低。两方面综合作用的结果,使窑内高温带缩短,液相出现迟,圈体部位长时间冷却剥落,最终消除。通过对TD炉处理窑内结圈的成功事例及两个炉子切换后参数的变化情况进行分析,笔者认为N-MFC炉煅烧频繁结圈的主要原因是:当使用N-MFC炉煅烧时,大部分物料入N-MFC炉,炉列阻力大,窑内通风相对增加,由于TD炉下缩口尺寸偏大,三次风门无法调节窑炉风量的平衡,造成烧成带风速过快;同时,由于煤质差,篦冷机冷却效果差,二次风温低,以及使用传统的三风道喷煤管,一次风量大,造成窑内煤粉燃烧速度慢。一方面是烧成带风速过快,煤粉燃烧速度慢,造成烧成带温度下降,火焰延长,高温带后移;另一方面是分解炉增容改造后,入窑物料分解率大幅度提高。两方面综合作用的结果,使回转窑烧结能力不足,预烧能力过强,物料在窑内过早出现液相而形成长窑皮。在实际处理过程中,由于入窑生料成份、煤质的波动及操作的不统一,造成窑内热工制度不稳定,使后部窑皮逐渐增厚而形成圈体。
成浇注料剥落。重新浇注时,将下缩口的尺寸改为∮950mm。投料运行后,通过优化操作参数(见表3),统一三班操作,稳定入窑生料成份,稳定煤质等措施,使熟料质量明显改善,熟料台时产量稳定在40.5t/h左右,窑内结圈、预热器堵塞、烟室结皮等工艺事故大大减少。
2、升温过快,窑皮拉长,处理不当停窑。(2001.4)
升温过快,预热器及N-MFC炉未能充分预热,就开始投料,因预热器分解炉系统与物料同时吸热,热耗高,用煤量大被迫拉大风,由二、三次风温低,喂料量短时间内加不到正常值,造成大量煤灰掺入,改变入窑物料成分,窑前入窑二次风量大、风温低,火焰长,物料过早出现液相,有时投料8小时,窑皮就长到28米左右;另一方面:前煤使用烟煤,热值波动大,当煤质变差时,前煤用量没有及时补充,造成窑前温度降低,火焰延长,而操作人员为维持窑产量的稳定,而这部分应应该窑前的煤加到了分解炉内,TD炉下缩口调整年,炉内通风足,炉容大,当增加后煤,使入窑物料分解率过高,物料入窑后过早出现液相,使窑皮拉长,后窑口开始有倒料现象。而在处理结圈倒料时,认为前煤用量大,易在窑内产生还原气氛,加重窑内结圈,在操作上,只减前煤,不减料,使前后煤比例失调,在喂料量不变的情况下,窑热工制度不易稳定,反而使结圈更为严重,被迫停窑处理,2002年12月份,虽然煤质差,但通过调整升温投料操作,增加前煤用量,始终将前后煤比例控制在40~45:60~55的范围侧,严格控制生料喂料在70t/h左右,统一操作参数,基本上消除结圈的现象。窑前结圈一般先是窑皮拉长,由于热工制度不稳定,而使后部窑皮增厚形成圈体。一旦形成圈体,火焰缩短,火焰很难处理,而热工制度波动时,窑温低时,被迫减料,偏高入窑物料分解率,
大料过后,窑内吸热减少,二次风温降低,火焰延长,使圈体部位温度上升,出液相;当电流上升时,开始增加料量,入窑物料分解率相对下降,火焰缩短,入窑物料出现液相位置推迟,在圈体易出现的液相表面,粘附一层低温料,增厚一层。在处理结圈时前煤减少过多,减料是一种不正确的做法。系统预热不好,增加煤耗,煤灰的大量掺入造成入窑物料过早出现液相,出窑熟料少,结粒粗,出窑熟料温度低,造成二次风温低,且窑内拉风大,造成火焰长,两者相互作用,在一班次之内造成窑皮拉长,加上我公司后窑口无缩口,当窑内填充率高时,后窑口产生倒料,污染大,采用煤管变动,冷热交换煅烧,往往是中间23~16之间的窑皮垮落而23~29m处窑皮始终不垮落,处理不好,反而造成窑况恶化最终停窑处理。升温过程中,系统预热不好,料少,煤多,煤灰掺入量大,造成窑皮拉长倒料,在处理的时方法不当,结圈严重。在系统风量受到限制时,增加料量造成窑内火焰缩短,料量过大,造成窑况不稳定,时而加料,时而减料,窑内火焰时长时短,主窑皮后部增厚,易造成结圈结球。窑皮拉长,不易掉,当条件成熟时,如生料成份波动大,操作不稳定,煤质波动等因素造成热工制度不稳定时,逐渐增厚而形成圈体。造成窑皮拉长,加之后窑口无缩口,当窑皮拉长,料量大时,填充率大,引起倒料在处理时,方法不对,而引起结圈加重而最终停窑解决的根本方法是:狠抓点火升温的投料操作;
冶标的方法是:稳定煅烧,控制风煤料适当,缩短火焰,使其长时间冷却,最终垮落。
3、前煤用量少,煤质差,后煤用量大,分解率过高是造成窑结圈的主要原因:(2000.6)
窑内通风大,前煤风量少,后煤用量大,入窑物料分解率过高,造成结圈,
窑内通风小,后煤用量大,入窑物料分解率过高造成结圈;
4、窑内用风过少,料量大,热工制度不稳定。(2002.1~4)
三、结圈的处理
1、16米以内的圈可以热烧,可适当放粗煤粉细度。
2、16~25米处,可以冷热交替;
3、25米以外的圈以冷烧为主;对于25~30米处结圈,因其结构疏松,抗热烧能力强,膨胀较
少,抗冷烧能力差,温度低不易烧掉;
四、预防措施:
如煤质、料量变化不大,热工制度稳定时,应该说窑皮是稳定;
1、稳定入窑生料成份及喂料量;
2、稳定煤质及喂煤量;
3、注意升温投料的操作;
4、控制合理窑炉用风比例及前、后煤的比例,控制最佳的烧结与预烧的平衡;
5、稳定窑电流在一定的范围内,窑电流的高低,可以衡量窑内温度的高低,出现液相的多少,
烧成带的温度,及时调整风、煤、料、窑速,控制回转窑内合理的热工制度是完全可以避免结圈、结球的。结合窑电流线的粗细,电流高低,熟料结粒的大小,可以判断窑内温度的高低与物料易烧性的适应性,窑电流线粗,熟料结粒粗,可以判断窑内温度对正在煅烧的物料较高,窑电流线细,熟料结粒细,可以判断物料煅烧需要的温度高,而火焰温度低,出现液相不足。窑电流线细,电流高,熟料结粒碎,可判断窑内温度偏低,烧成带长,窑电流粗,电流高,熟料结粒大,判断窑内温度高,烧成带长。