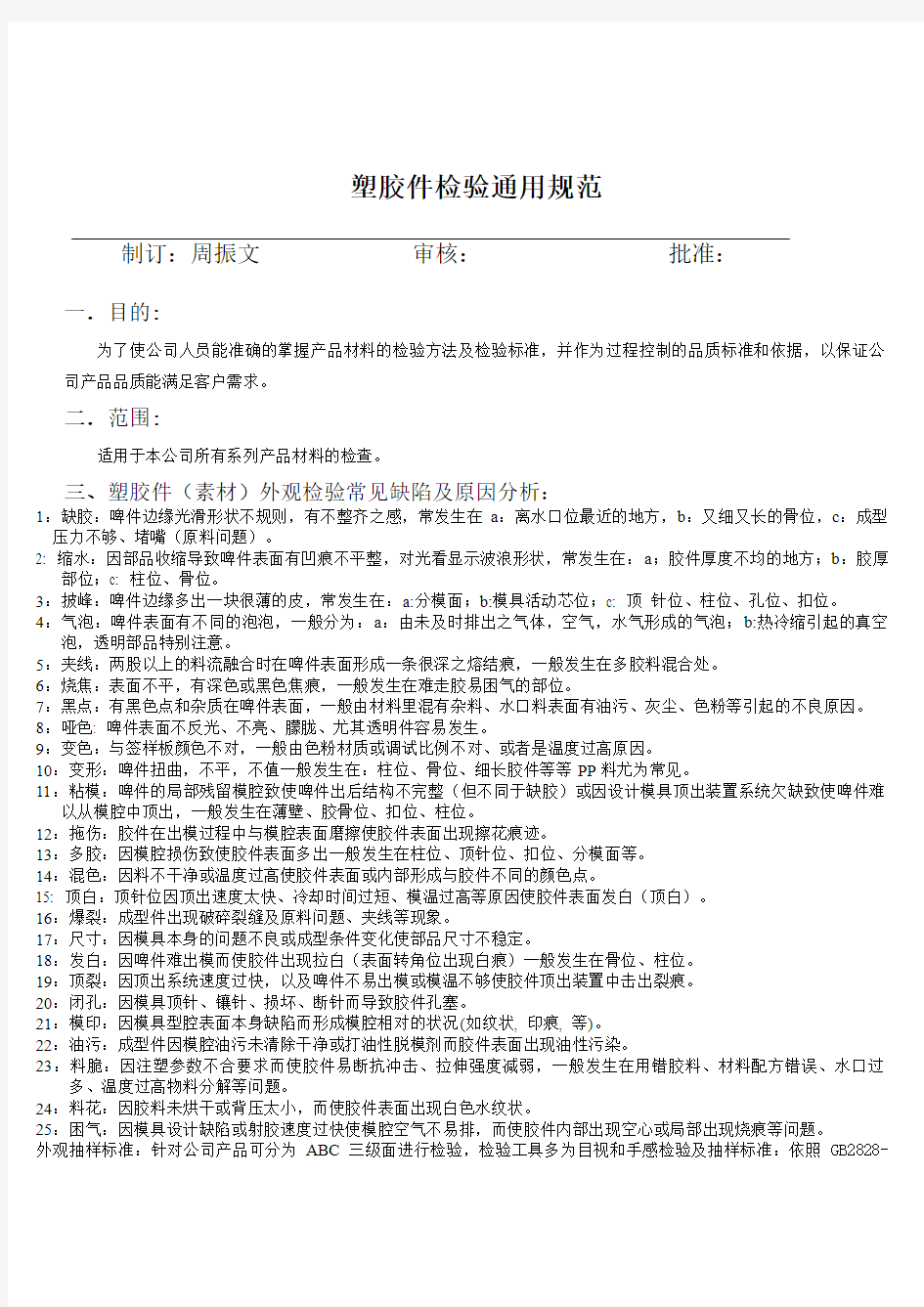
塑胶通用检验规范
- 格式:doc
- 大小:35.00 KB
- 文档页数:3
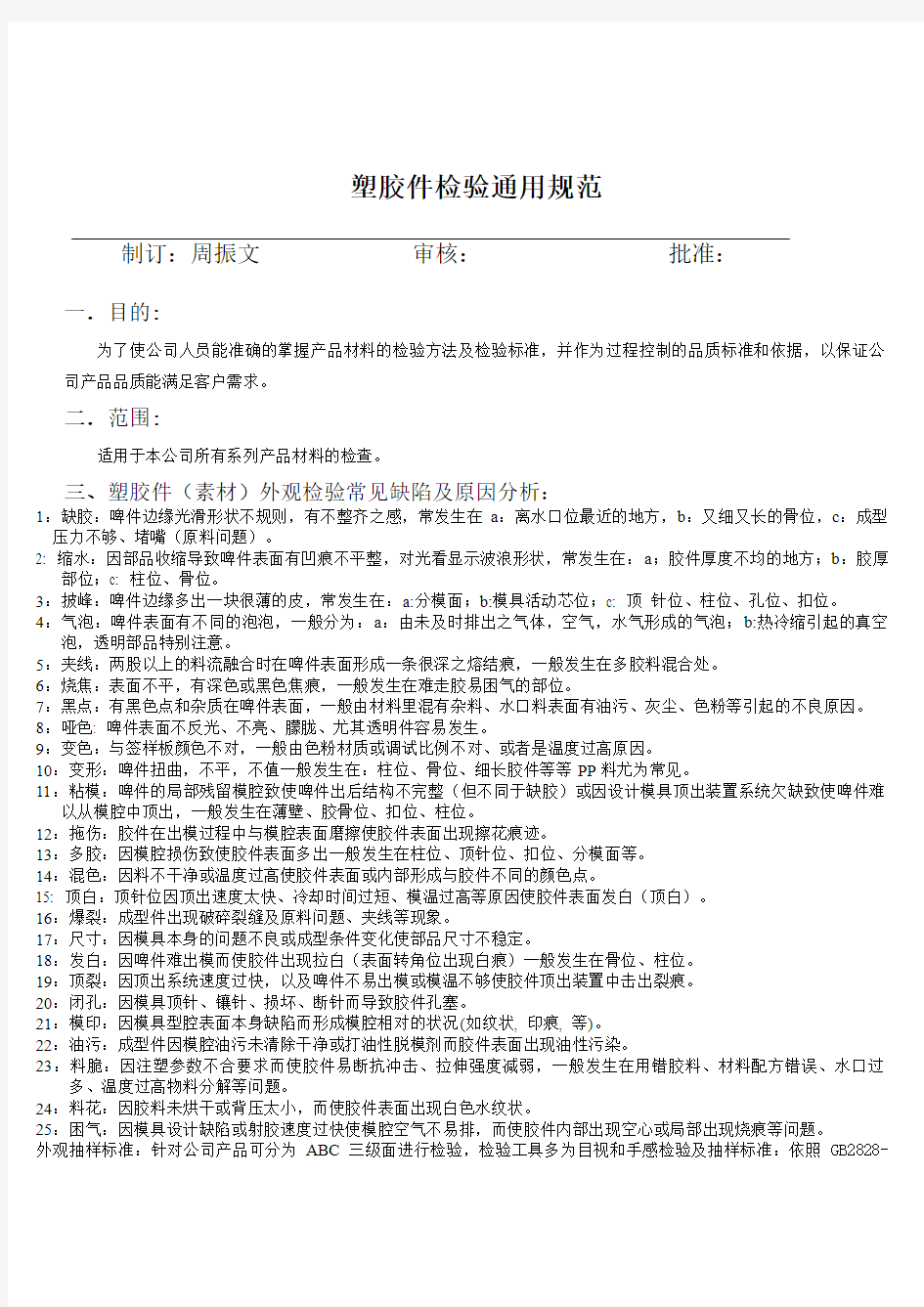
塑胶件检验通用规范
制订:周振文审核:批准:一.目的:
为了使公司人员能准确的掌握产品材料的检验方法及检验标准,并作为过程控制的品质标准和依据,以保证公司产品品质能满足客户需求。
二.范围:
适用于本公司所有系列产品材料的检查。
三、塑胶件(素材)外观检验常见缺陷及原因分析:
1:缺胶:啤件边缘光滑形状不规则,有不整齐之感,常发生在a:离水口位最近的地方,b:又细又长的骨位,c:成型压力不够、堵嘴(原料问题)。
2: 缩水:因部品收缩导致啤件表面有凹痕不平整,对光看显示波浪形状,常发生在:a;胶件厚度不均的地方;b:胶厚部位;c: 柱位、骨位。
3:披峰:啤件边缘多出一块很薄的皮,常发生在:a:分模面;b:模具活动芯位;c: 顶针位、柱位、孔位、扣位。
4:气泡:啤件表面有不同的泡泡,一般分为:a:由未及时排出之气体,空气,水气形成的气泡;b:热冷缩引起的真空泡,透明部品特别注意。
5:夹线:两股以上的料流融合时在啤件表面形成一条很深之熔结痕,一般发生在多胶料混合处。
6:烧焦:表面不平,有深色或黑色焦痕,一般发生在难走胶易困气的部位。
7:黑点:有黑色点和杂质在啤件表面,一般由材料里混有杂料、水口料表面有油污、灰尘、色粉等引起的不良原因。8:哑色: 啤件表面不反光、不亮、朦胧、尤其透明件容易发生。
9:变色:与签样板颜色不对,一般由色粉材质或调试比例不对、或者是温度过高原因。
10:变形:啤件扭曲,不平,不值一般发生在:柱位、骨位、细长胶件等等PP料尤为常见。
11:粘模:啤件的局部残留模腔致使啤件出后结构不完整(但不同于缺胶)或因设计模具顶出装置系统欠缺致使啤件难以从模腔中顶出,一般发生在薄壁、胶骨位、扣位、柱位。
12:拖伤:胶件在出模过程中与模腔表面磨擦使胶件表面出现擦花痕迹。
13:多胶:因模腔损伤致使胶件表面多出一般发生在柱位、顶针位、扣位、分模面等。
14:混色:因料不干净或温度过高使胶件表面或内部形成与胶件不同的颜色点。
15: 顶白:顶针位因顶出速度太快、冷却时间过短、模温过高等原因使胶件表面发白(顶白)。
16:爆裂:成型件出现破碎裂缝及原料问题、夹线等现象。
17:尺寸:因模具本身的问题不良或成型条件变化使部品尺寸不稳定。
18:发白:因啤件难出模而使胶件出现拉白(表面转角位出现白痕)一般发生在骨位、柱位。
19:顶裂:因顶出系统速度过快,以及啤件不易出模或模温不够使胶件顶出装置中击出裂痕。
20:闭孔:因模具顶针、镶针、损坏、断针而导致胶件孔塞。
21:模印:因模具型腔表面本身缺陷而形成模腔相对的状况(如纹状, 印痕, 等)。
22:油污:成型件因模腔油污未清除干净或打油性脱模剂而胶件表面出现油性污染。
23:料脆:因注塑参数不合要求而使胶件易断抗冲击、拉伸强度减弱,一般发生在用错胶料、材料配方错误、水口过多、温度过高物料分解等问题。
24:料花:因胶料未烘干或背压太小,而使胶件表面出现白色水纹状。
25:困气:因模具设计缺陷或射胶速度过快使模腔空气不易排,而使胶件内部出现空心或局部出现烧痕等问题。
外观抽样标准:针对公司产品可分为ABC三级面进行检验,检验工具多为目视和手感检验及抽样标准:依照GB2828-
03 /IL=Ⅱ执行,允收水准为:CR:致命缺陷为:0 MA:严重缺陷为:0.65 MI:轻微缺陷为:2.5。
检验方法:目视检验:针对产品表面进行目视(20-30CM,光照度60以上)观察检验,此方法对外观检验使用
最
多。手感检验:对产品表面无法用肉眼进行观察,但可用手进行触摸的使用手动感觉检验。试喷检验:针对后续需
要
进行喷涂或电镀作业的素材,可行进行试喷和试电镀作业确认检验,判定素材对喷涂有无影响,此方法可由喷油厂
或
素材供应商协助试喷送样确认。5注意事项:1素材部份出现的披峰,变形,刮伤,水口位清除不良,缺胶,材质差等问题对后续的装配及二次加工都会产生严重的不良
影响,需要在素材部份就重点控制住,不可流入后面工序中再来控制,(例如:素材LCD固定框注塑时有严重披峰,所用材料材质易
碎,
检验时未有发现和清除,外发喷油后因存在披峰和材质问题,披峰与油墨固化在一起,清除极其困难,而且披峰的存在导致尺寸无法测量准确,组装过程中LCD玻璃无法装到位,这就是因为素材部份披峰未清除导致后面的几道工序都出现问题,而材质易碎则在锁螺丝
时
出现螺丝柱开裂现象,如果在素材部份就控制这些问题,那在后面的工序中就不会出现像上现这样的异常问题,异常处理成本就非常
高)
这主说明素材部份要控制的重点非常重要。
2正确的测量方法和正确的测量工具才是保证测量正确性的重点。(例如:在测量一个齿轮,齿轮的孔径只有 1.5MM,但检验人员使用卡尺对齿轮孔径进行测量,测出数量为1.45MM标准为1.5MM+0/-0.02MM判定不合格,但实际使用1.48MM的棒规测试可以通过,实配也OK,这就说明卡尺测量1.5MM孔径是不可取的,正确的测量工具应该是棒规,只有这样才能保证测量的正确性。)
四、塑胶尺寸检验方法:
1.尺寸检验:找到相关键的资料及工具如:工程蓝图、样板、测量仪器(卡尺、棒规,塞规)等等。针对工程蓝图的
重要尺寸管控及测量,
2.检验及抽样标准:依产品设计图纸所标注之尺寸公差进行测量验证,由于塑胶件素材尺寸是由模具所决定,注塑时
对尺寸变化非常小,易变化的多为细小部份,所以抽样数每批抽取5PCS就可完成对尺寸的确认,允收水准0收1退检验方法:直尺测量:针对精密度要求不高,卡尺无法测量的尺寸使用直尺进行检验卡尺测量:针对精密度要求在0.02~0.2MM的尺寸可以使用卡尺进行测量尺寸进行测量检验,小于5MM的孔径除外棒规测量:针对精
密
度要求在0.02~0.2MM小于5MM的孔径尺寸使用棒规测量检验。塞规测量:针对有密合要求的元件使用塞
规
进行测量检验。
五、材质检验标准:
1.材质部份:主要针对塑胶件所用材质进行确认,主要不良为水口料使用过多,次级料充当优级料,注塑成型时参数
未调好,造成注塑成型的缺陷(如缩水,分层等)其检验工具有:冲击测试治具,剪钳,电批
2.检验及抽样标准:依设计图纸中元件材质要求进行验证,同批产生的元件使用的材料相同,此时随机从批量中抽出
1PCS来进行验证即可控制,如果交进批量中有不同时间生产的,可按生产时间进行分期抽检,但因为材质检验多为破损性测度,成本考量,小批量或同期生产抽检1PCS,大批量或多期生产的抽检2PCS,允收水准都是0收1退。
3.检验方法:冲击检测:针对表面易受到冲击的素材使用冲击测试治具进行冲击破坏,检验材料融合是否良好,是否
有次级材料充当优级材料现象,出现开裂,易碎,变形严重的现象。此方法多用在面盖,底座的检验。
4.破坏检验:针对重点的基础件(基础件:与多种元件配合,元件都以此元件为基座的塑胶元件我们称为基础件)用
钳子或锤子进行破坏,对破坏面进行检验确认,此检验方法是材质检验的最常用的检验方法。
5.试锁检验:针对有螺丝柱的塑胶件使用对应的螺丝用电批模拟正常操作对塑胶件螺丝柱进行试锁检验
6.寿命检验:针对常时间运行的元件(如齿轮、蜗杆、活动支架等)可将元件装入总成中进行寿命跑机检验咬合状
况,以及磨损效果,此检验方法多用在样品评估或新供应商开发,以及周期性确认检验中,正常检验中不做考虑。
六、试装检验标准:
1.装配部份:主要针对塑胶元件与其相配合的其他元件间的组装配合性能进行检验
2.检验及抽样标准:依产品设计爆炸图中元件关系执行,与试装元件有配合关系的相邻的一个或两个元件之间试配
无影响。同类产品制作工艺相同每批随机抽取1PCS进行测试即可。
3.检验方法:试装检验:将待检验元件与一个或两个与待检元件有装配关系的元件进行试装检验,验证元件间配合
有