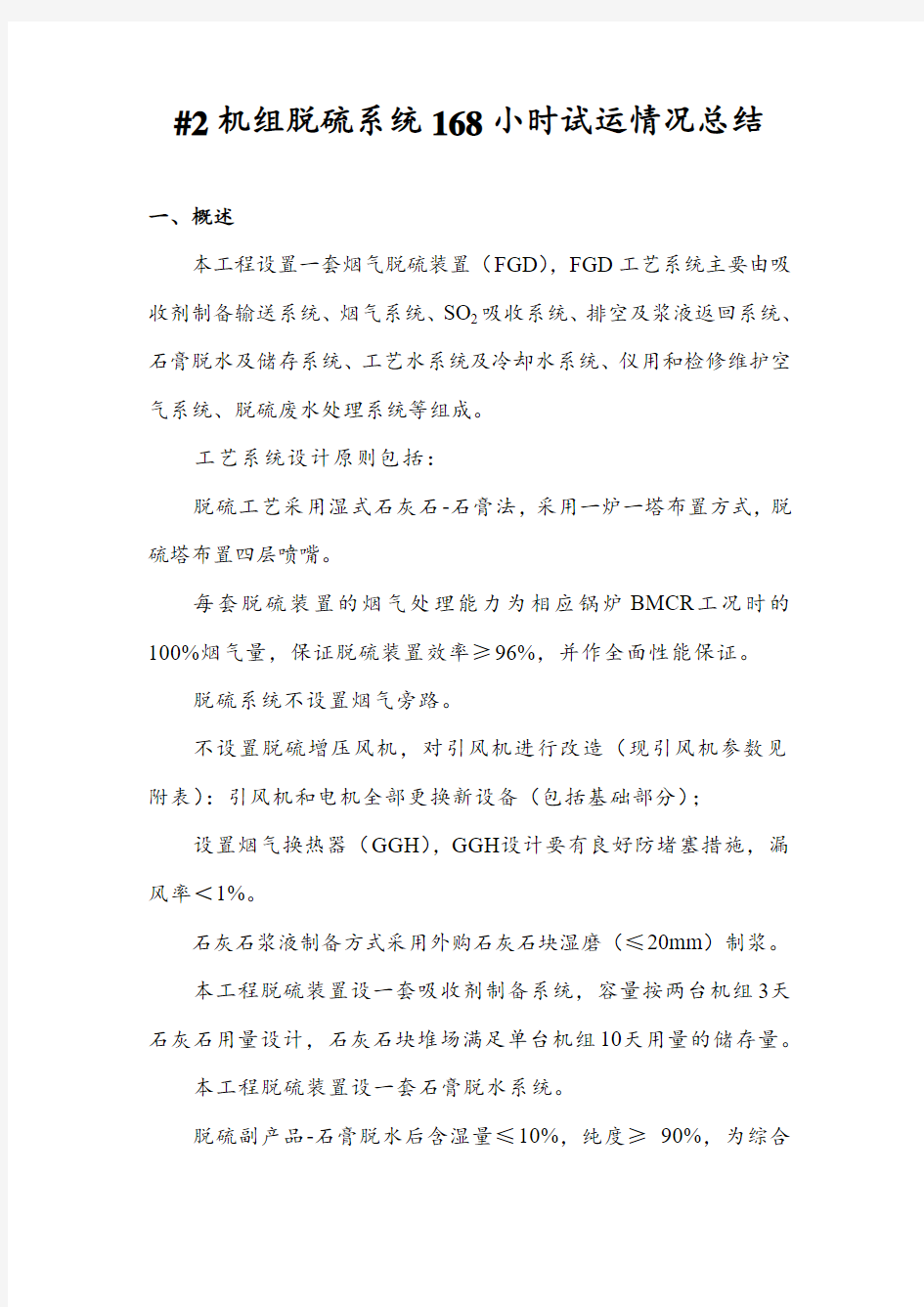
_2机组脱硫168试运汇报
- 格式:docx
- 大小:37.17 KB
- 文档页数:9
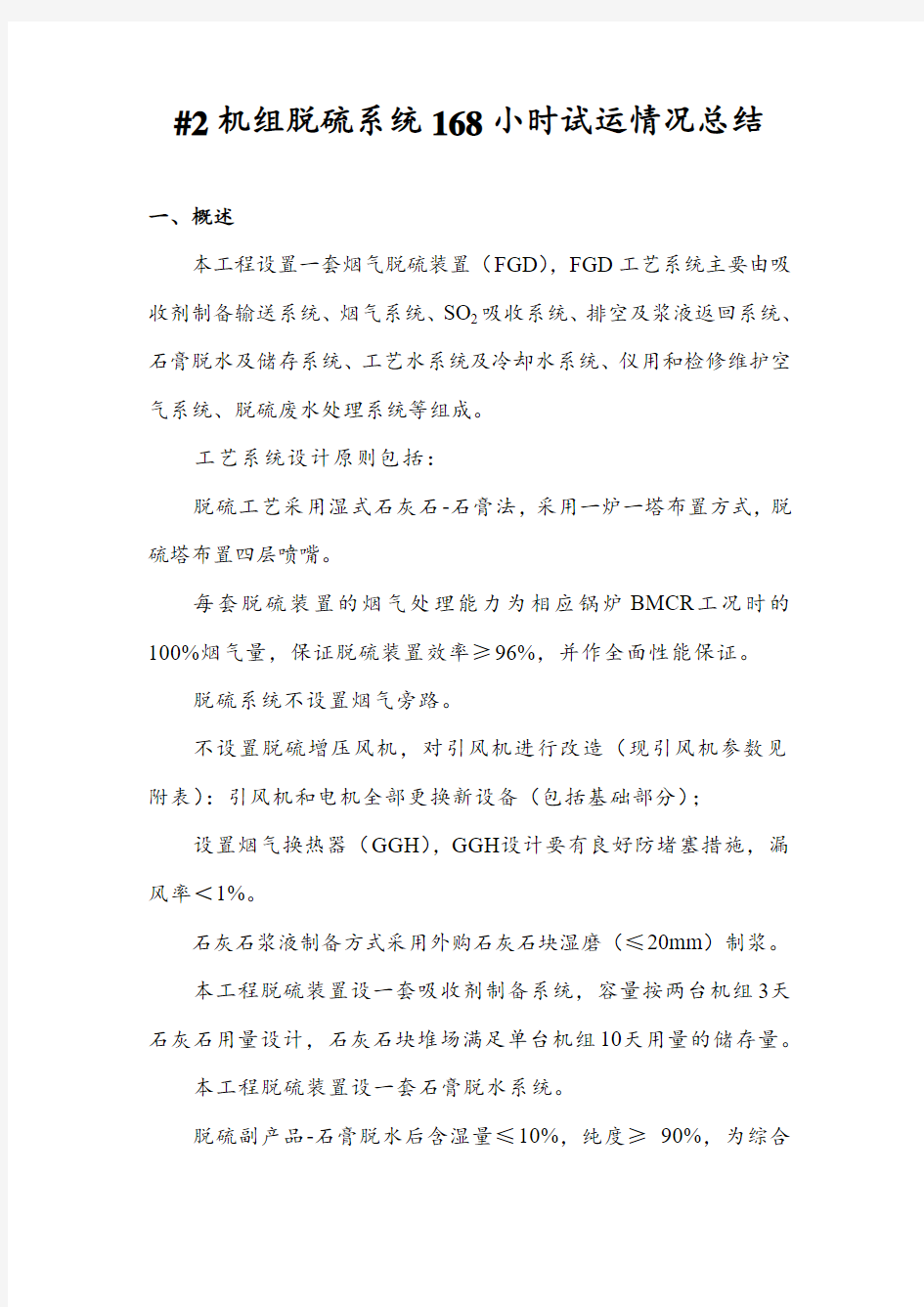
#2机组脱硫系统168小时试运情况总结
一、概述
本工程设置一套烟气脱硫装置(FGD),FGD工艺系统主要由吸收剂制备输送系统、烟气系统、SO2吸收系统、排空及浆液返回系统、石膏脱水及储存系统、工艺水系统及冷却水系统、仪用和检修维护空气系统、脱硫废水处理系统等组成。
工艺系统设计原则包括:
脱硫工艺采用湿式石灰石-石膏法,采用一炉一塔布置方式,脱硫塔布置四层喷嘴。
每套脱硫装置的烟气处理能力为相应锅炉BMCR工况时的100%烟气量,保证脱硫装置效率≥96%,并作全面性能保证。
脱硫系统不设置烟气旁路。
不设置脱硫增压风机,对引风机进行改造(现引风机参数见附表):引风机和电机全部更换新设备(包括基础部分);
设置烟气换热器(GGH),GGH设计要有良好防堵塞措施,漏风率<1%。
石灰石浆液制备方式采用外购石灰石块湿磨(≤20mm)制浆。
本工程脱硫装置设一套吸收剂制备系统,容量按两台机组3天石灰石用量设计,石灰石块堆场满足单台机组10天用量的储存量。
本工程脱硫装置设一套石膏脱水系统。
脱硫副产品-石膏脱水后含湿量≤10%,纯度≥90%,为综合
利用提供条件。
石膏储存采用石膏仓库方案,石膏仓容量按两台机组2天石膏产量设计。
脱硫设备年利用小时按6000小时考虑。
FGD系统可用率≥98%。
FGD装置服务寿命为30年。
二、试运情况汇报
我公司#2机组脱硫系统168小时运行于2015年1月24日8:00开始计时,至1月31日8:00试运完成,各辅机及系统运行基本正常,具体情况如下:
(一)SO2浓度排放情况:
脱硫168调试因电网负荷限制,最高调试负荷为250MW,平均负荷在206MW,#2机发电量3440.8万kw.h,#2炉在脱硫系统168期间燃煤总量22313吨,平均硫份1.07%,平均脱硫效率98.61%,高于系统设计值96%,投运率100%,SO2小时平均排放浓度45.62mg/m3,SO2总减排量约375.17吨,满足环保排放要求;其中耗石灰石983吨,钙硫比1.20,高于设计值1.03,石灰石利用率约为83.3,低于设计值90%,具体如下表所示:
(二)保护自动投入情况
1、各区域排水坑系统液位与泵的启停联锁自动投入。
2、投入的保护有:
1)#2脱硫主联锁保护:浆液循环泵全停或GGH两台驱动电机全停,#2炉发BT。
2)原烟气事故喷淋阀与原烟气温度联锁保护投入。
3)浆液循环泵、氧化风机、制浆系统、脱水系统及石灰石上料系统联锁保护。
(三)程控投入情况
现场所有电动控制设备基本上能实现远程操作(事故返回泵入口阀及石膏排出泵A入口阀除除外,这两电动阀在调试期间出现故障)。(四)各系统运行情况简介
1、石灰石浆液制备系统运行情况
磨机入口研磨水量3.5t/h,石灰石给料10.2t/h,稀释水量21t/h,料水比约为1:2.5,石灰石旋流站压力在0.08Pa左右,旋流子投入四颗,石灰石浆液密度维持在1200~1250kg/m3之间,浆液品质合格;磨机主电机电流在35.2A左右,空转电流34.1A,磨机润滑油低压油
压力0.2MPa左右,高压油压力大于4.5MPa,滤网前后压差0.02MPa(高于0.05MPa报警),运行状况良好。石灰石浆液旋流站分配电动推杆限位开关坏,DCS上状态反馈错误,经就地检查,其自动动作正常;磨机减速机油泵流量开关处漏油,且流量反馈异常(压力正常信号不来,就地流量正常),上述缺陷已于2月份处理好。
2、脱水系统运行情况
脱水效果良好,脱水机频率在60%左右,滤饼厚度在20~25mm 之间,含水率10%~15,石膏纯度大于90%,达到设计标准。石膏旋流站旋流子运行5颗,备用一颗,就地压力0.12MPa,底流浓度约55%,分离效果良好。真空泵运行电流135~149A之间,在140A左右时脱水效果最好。
因石膏旋流站溢流与气液分离器回流管连接在一起回至滤液水箱,石膏旋流站运行时,因溢流压力过高,致使气液分离器回流不畅,气液分离器多次出现过料位高报警,并进一步导致真空泵输水带浆进入工艺水箱,后经与国信、生技部现场考察,制定解决方案,决定对该处管道进行改造,改造工作已于2月23日结束,现运行状况良好。
3、吸收塔系统运行情况
吸收塔运行液位保持在7.5m左右,最高液位在8.5m,因吸收塔区冷却水回水不畅,为了保证设备正常运行,将氧化风机冷却水回水割开,这部分水通过浆液循泵区域地沟回至脱硫系统,给脱硫系统水平衡控制带来了一定困难,在加上废水系统未正式投入运行,致使脱硫系统在低负荷时(低于160MW),水平衡难以控制。正常运行时,
脱硫浆液PH值控制在5.0~5.8之间,密度控制在1080~1150kg/m3之间,浆液密度高于1100kg/m3时,投入脱水系统运行。吸收塔PH计安装不合理,使得运行时磨损严重,使用寿命短,且不易冲洗,经与设备部和工程部碰头协商后,已经对其进行改造,现阶段运行状况良好,电极使用寿命明显变长。
浆液循环泵运行状况基本稳定,减速机、轴承、电机线圈等重要部位温度在正常范围内运行,出口压力及流量达到设计要求,满足运行需求。负荷在200MW左右,吸收塔PH值控制在5.0~5.4:①原烟气S02浓度低于2000mg/m3时,循泵A、B运行即可满足排放要求,排放值在70mg/m3左右;②原烟气SO2浓度在2500~3000 mg/m3时,需要运行3台浆液循泵(A、B、C)才能满足排放要求,排放值在50mg/m3左右;③原烟气S02浓度在3000~4500 mg/m3时,浆液循环泵B、C、D或者A、C、D运行才能达到排放要求,排放浓度低于15~30mg/m3;④原烟气SO2高于4500mg/m3时,4台浆液循环泵运行勉强能达到排放要求,因为原烟气浓度远高于设计值(4000mg/m3),为了保护脱硫系统及保证系统正常供浆量,需联系值长投入炉内脱硫系统,配合炉外脱硫系统对烟气进行处理。
氧化风机能满足浆液氧化所需空气量要求,其基本工况如下:
入口挡板开度在38%左右,氧化空气压力60KPa,流量大于9000m3/h(9000~10000m3/h间),电机电流29~31A。
运行时需要认真调整氧化空气增湿水量,避免增湿水开度过大,导致吸收塔水平衡难以控制;同时也预防增湿水开度过小,导致氧化