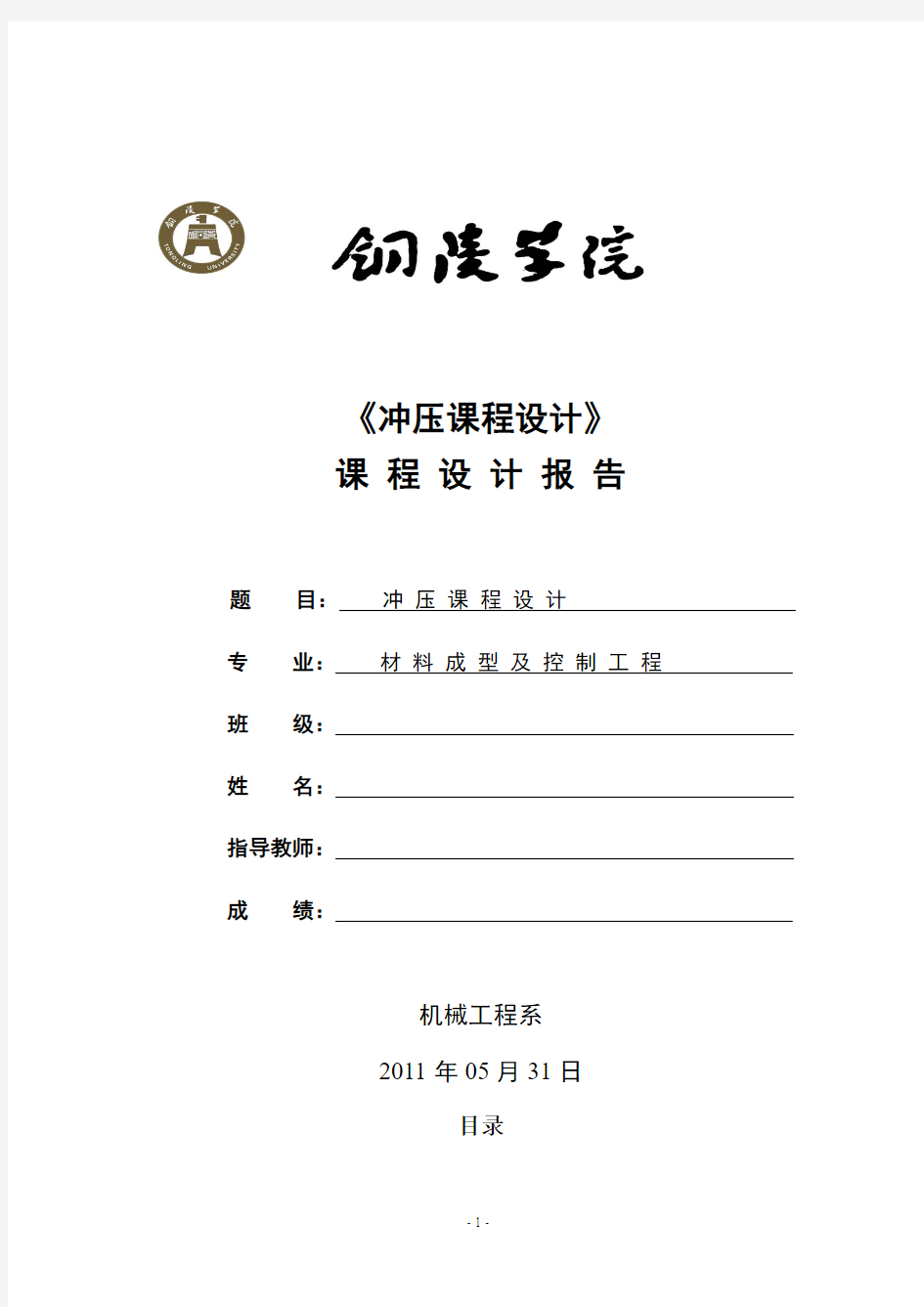
-冲压课程设计
- 格式:doc
- 大小:472.00 KB
- 文档页数:14
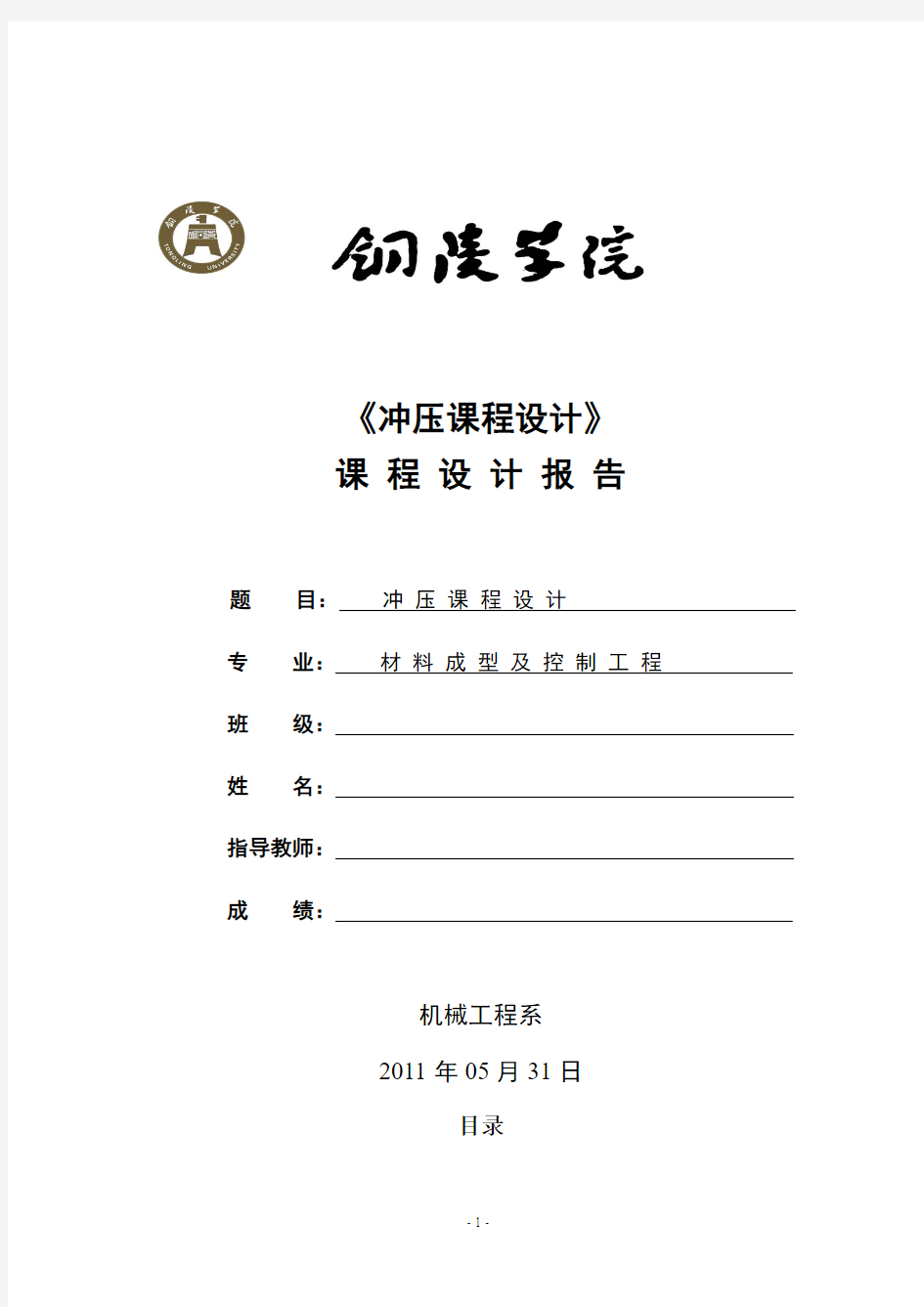
《冲压课程设计》
课程设计报告
题目:冲压课程设计
专业:材料成型及控制工程班级:
姓名:
指导教师:
成绩:
机械工程系
2011年05月31日
目录
摘要 (3)
第一章零件的工艺性分析 (4)
1.1产品结构形状分析 (4)
1.2产品尺寸精度、粗糙度、断面质量分析 (4)
1.3产品材料分析 (4)
1.4分析产量 (4)
第二章生产方案的制定 (4)
2.1单工序逐步加工 (5)
2.2复合模加工 (5)
2.3连续模加工 (5)
第三章冲模结构的确定 (5)
3.1模具的形式 (5)
3.2定位装置 (6)
3.3卸料装置 (6)
3.4导向零件 (6)
3.5模架 (6)
第四章排样设计 (6)
4.1单排 (6)
4.2交叉双排 (7)
第五章压力中心计算 (8)
5.1计算模具压力中心 (8)
第六章冲压工艺力计算 (9)
6.1冲裁力的计算 (9)
6.2冲孔冲裁力 (9)
6.3落料冲裁力 (10)
6.4卸料力 (10)
6.5推料力 (10)
6.6顶件力 (10)
6.7总冲压力 (10)
6.8压力机选择 (11)
第七章刃口尺寸计算 (11)
7.1冲孔凸凹模计算 (11)
7.2落料凸凹模计算 (11)
小结 (13)
参考文献 (14)
《塑性成型工艺(冲压)》课程设计说明书
摘要
冲压模具在实际工业生产中应用广泛。在传统的工业生产中,工人生产的劳动强度大、
劳动量大,严重影响生产效率的提高。随着当今科技的发展,工业生产中模具的使用已经越来越引起人们的重视,而被大量应用到工业生产中来。冲压模具的自动送料技术也投入到实际的生产中,冲压模具可以大大的提高劳动生产效率,减轻工人负担,具有重要的技术进步意义和经济价值。
此次课程设计对制件的冲压工艺进行了分析,冲压工艺方案及模具的结构类型进行了确定,并进行了必要的冲压工艺参数计算及模具工艺零件与结构零件的选用。为了增大材料的利用率,减少工序复杂程度,设计了先冲孔后落料的级进模具。
在本次课程设计中利用计算机辅助设计(CAD)绘制模具主要工作排样图和模具的刃口尺寸图。
本次课程设计是一次对所学知识的全面总结和运用,是巩固和加深各种理论知识灵活运用的实践过程。
关键词:冲压;模具;冲压工艺;冲孔;落料;排样图
第一章冲压件的工艺分析
由图1 – 1 零件图
1.1产品结构形状分析
由图1 –1可知,产品为圆片落料、非圆片冲孔。产品形状简单对称,无下槽;孔与
零件边缘之间最小距离 c 满足 c 》1.5 t 要求。(c=
222
52
=15 1.5t=1.5×1.5=2.25)
1.2产品尺寸精度、粗糙度、断面质量分析
①尺寸精度。该零件所有尺寸都未标注公差,属于未标注公差尺寸,因此该零件在精度方面要求不高,很容易达到要求。
②冲裁件断面质量。因为一般用普通冲裁方式冲2mm以下的金属板料时,其断面粗糙度Ra可达12.5 ~ 3.2um,毛刺允许高度为0.01 ~ 0.05mm;本产品在断面粗糙度和毛刺高度上没有太严格的要求,所以只要模具精度达到一定要求,冲裁件的断面质量可以达到保证。
1.3产品材料分析
对于冲压件材料一般要求的力学性能是强度低,塑性高,表面质量和厚度公差符合国家标准。本设计的产品材料是Q235钢,属普通碳素钢,其力学性能、强度、硬度和塑性指标适中,用冲裁的加工方法是完全可以成形的。另外本产品对于厚度和表面质量没有严格要求,所以尽量采用国家标准的板材,其冲裁出的产品的表面质量的厚度公差就可以保证。
经上述分析,产品的采莲性能符合冷冲压加工要求。
1.4分析产量
产品批量为大批量,很适合采用冲压的加工方法,最好采用复合模或连续模,若能加上自动送料装置,会大大提高生产效率,降低成本。
第二章生产方案的制定
完成此工件需要冲孔、落料两道工序。其加工的工艺方案分为以下3种。
2.1单工序逐步加工
采用单工序逐步加工有两种方案
①冲孔、落料单工序模,工序简图见图2 – 1。
②落料、冲孔单工序模,工序简图见图2– 2。
特点:由于采用单工序模,模具制造简单,维修方便。但生产率低,工件精度低不适合大批量生产。
图2–1冲孔、落料单工序模图2–2落料冲孔单工序模2.2复合模加工
采用复合模加工成形工序简图见图2–3。
特点:生产率较高,工件精度高,但模具制造复杂,调整维修较麻烦,使用寿命低。
2.3级进模加工
采用连续模加工成形工序简图见图2–4。
特点:生产率高,便于实现机械化、自动化,但模具制造复杂,调整维修麻烦,工件精度较低。
根据本零件的设计要求,以及各方案的特点决定采用复合模比较合理。
图2–3冲孔、落料复合模图2–4冲孔、落料级进模
第三章冲模结构的确定
3.1模具的形式
复合模又可分为正装式和倒装式。
①正装式特点。工件和冲孔废料都落在凹模表面上,必须加以清除后才能进行下一次
冲裁,因此操作不方便,也不安全,对多孔工件不宜采用,但冲出的工件表面比较平直。
②倒装式特点。冲料由冲孔凸模冲入凹模洞口中,积累到一定数量,由下模漏料孔排出,不必清除废料,操作方便,应用很广,但工件表面平直度较差,凹凸模承受的张力较大,因此凹凸模的壁厚应严格控制,以免强度不足。
经分析,此工件有两个孔,若采用正装式复合模,操作很不方便,另外,此工件无较高的平直度要求,工件精度要求也低,所以从操作方便、模具制造简单等方便考虑,决定采用倒装式复合模。
3.2定位装置
采用伸缩式挡料销纵向定位,安装在下模座和活动卸料板之间。工作是可随凹模下行而压入孔内,工作很方便。
采用导料螺栓横向定位。因为它结构简单,使用方便,对模具强度削弱小。
3.3卸料装置
①条料的卸除。采用弹性卸料板。因为是倒装式复合模,所以卸料安装在下模。
②工件的卸除。采用打料装置将工件从上模落料凹模中推下,落在模具工作面上。
③冲孔废料的卸除。采用下模座上漏料孔排出。冲孔废料在下模的凹凸模内积聚到一定数量,便从下模座的漏料孔中排出。
3.4导向零件
导向零件有许多,如用导板导向,则在模具上安装不方便,而且阻挡操作者视线,所以不采用;若用滚珠式导柱导套进行导向,则虽然导向精度高,寿命长,但结构比较复杂,所以也不采用;针对这次加工的产品精度要求不高,采用滑动式导柱导套进行导向即可。而且模具在压力机上的安装比较简单,操作又方便,还可降低成本。
3.5模架
若采用中间导柱模架,则导柱对称分布,受力平衡,滑动平稳,拔模方便,但只能一个方向送料。若采用对角导柱模架,则受力平衡,滑动平稳,可纵向或横向送料。若采用后侧导柱模架,则可三方向送料。操作者视线不被阻挡,结构比较紧凑,但模具受力不平衡,滑动不平稳。
本设计决定采用中间导柱模架。
第四章排样设计
4.1单排
a.搭边。查《冷冲压工艺及模具设计》表2-9,确定搭边值a,b。
当t=1.5时a=2 b=1.5
b.条料宽度。采用无测压装置。所以
B=D+2a+Z
式中Z—导尺与最宽条料之间的最小间隙,查《冷冲压工艺及模具设计》表2-12得Z=0.5mm。
所以