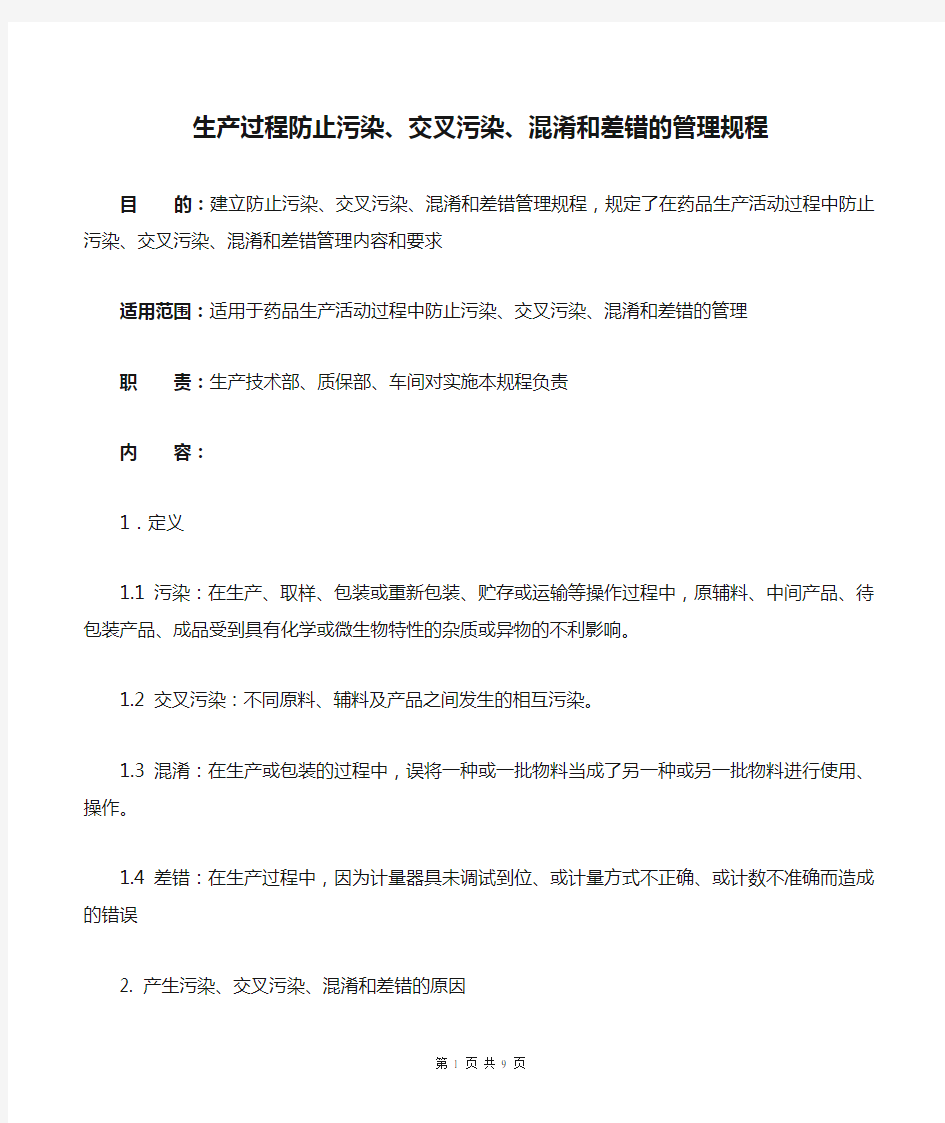
生产过程防止污染、交叉污染、混淆和差错的管理规程
- 格式:doc
- 大小:44.50 KB
- 文档页数:6
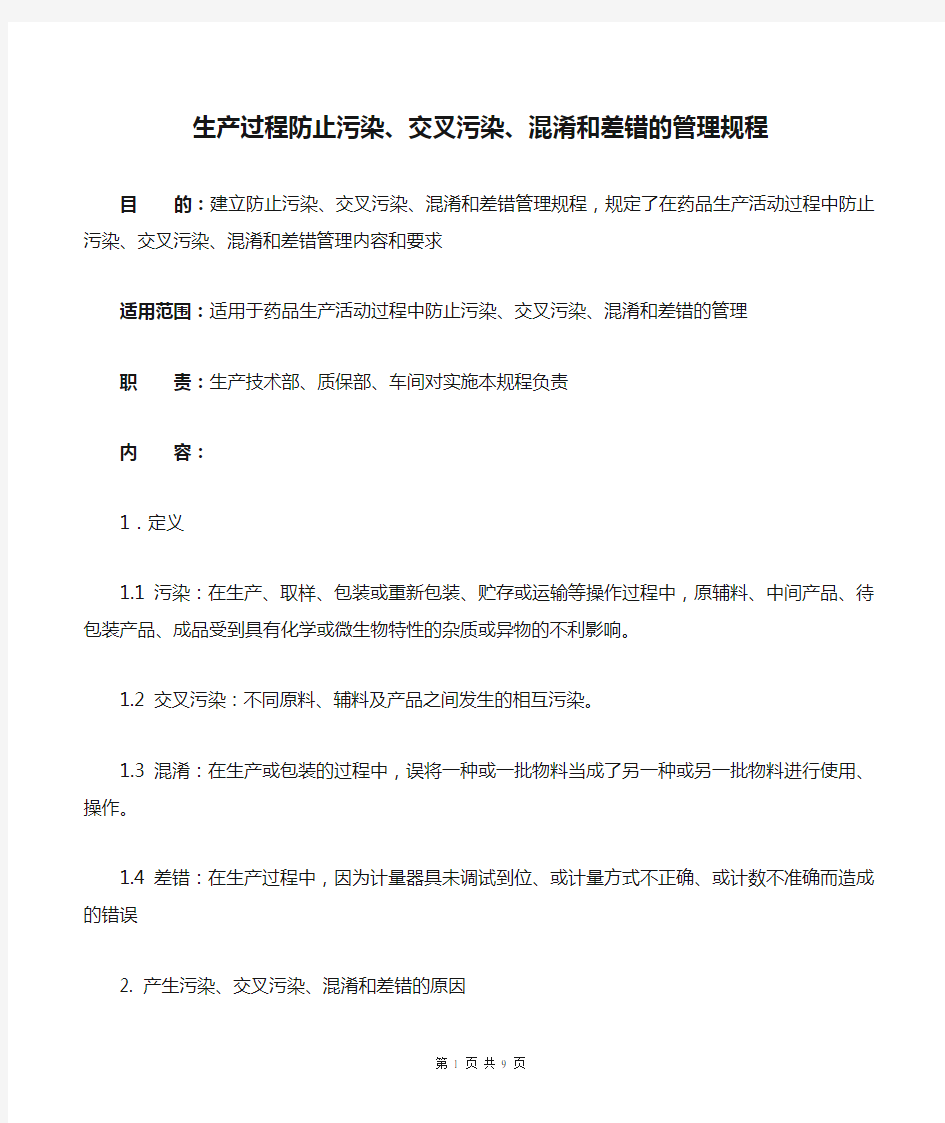
生产过程防止污染、交叉污染、混淆和差错的管理规程目的:建立防止污染、交叉污染、混淆和差错管理规程,规定了在药品生产活动过程中防止污染、交叉污染、混淆和差错管理内容和要求
适用范围:适用于药品生产活动过程中防止污染、交叉污染、混淆和差错的管理
职责:生产技术部、质保部、车间对实施本规程负责
内容:
1.定义
1.1污染:在生产、取样、包装或重新包装、贮存或运输等操作过程中,原辅料、中间产品、待包装产品、成品受到具有化学或微生物特性的杂质或异物的不利影响。
1.2 交叉污染:不同原料、辅料及产品之间发生的相互污染。
1.3混淆:在生产或包装的过程中,误将一种或一批物料当成了另一种或另一批物料进行使用、操作。
1.4 差错:在生产过程中,因为计量器具未调试到位、或计量方式不正确、或计数不准确而造成的错误
2. 产生污染、交叉污染、混淆和差错的原因
2.1 人员:操作人员患有传染病、皮肤病等,或未接受卫生方面的培训,未按要求穿戴工作服,行为不规范、人员带来外部污染,生产人员未按工艺规程和SOP要求操作,工作责任心不强,工作量过大,操作中随意性大等。
2.2 设备:表面不光洁、平整,材质不稳定,不易清洁,设备选型不合理,维修、保养不及时,没有定期验证或没有保持验证状态。生产中使用的设备、容器无状态标志,清场不彻底等造成混淆。
2.3 物料:购进的原辅料本身质量不好,或在运输、贮存、检验取样、配料过程中造成污染。原辅料微生物指标超限。原辅料、包装材料、半成品、中间体等无明显标志,放置混乱,散装或放在易破损的包装中,印刷性包装材料管理不善等。
2.4 文件:文件管理制度不健全,或执行不力,无复核、监控,发现问题未及时查找原因等,特别是配料、包装等重要部门管理不严格。
2.5 环境:厂房设计不合理,生产环境如空气中粒子过多,车间地面、墙壁、天花板等不平整、易脱落、长霉、消毒不严格等造成污染。
2.6 清洁:清洁效果不能保证微生物除去水平及残留限度,清洁剂残留、消毒剂效果不
能保证;生产结束后不及时清洁清场等造成污染。
2.7 生产过程:生产过程控制不规范,生产中敞口生产,密闭不严,管道中有死角,生产周期过长,操作不当等。
3. 防止污染、交叉污染、混淆和差错的措施
生产过程中产生污染、交叉污染、混淆和差错的可能随时存在,必须在全过程各个环节都加强管理和监控。除了对生产中人员、设备、物料、文件、环境、清洁等引起污染、交叉污染、混淆和差错的因素进行控制外,还要采取相应的措施。
3.1 人员
3.1.1 所有人员都应接受卫生方面的培训后上岗,熟练掌握生产区域人员更衣、卫生操作,最大限度地降低人员对药品生产造成污染的风险。
3.1.2 当对人员健康进行管理,并建立健康档案。直接接触药品的生产人员上岗前应当接受健康检查,以后每年至少进行一次健康检查。
3.1.3 禁止体表有伤口、患有传染病或其他可能污染药品疾病的人员从事直接接触药品的生产。
3.1.4 选用洁净服材质符合要求,洁净服穿戴符合规范。
3.1.5员工按操作规程办事,按规定如实填写记录、遇事及时汇报上级等,最大程度地防止发生混药混批。
3.1.6 外来人员必须经过批准并在指定人员的陪同及指导下方可进入车间。
3.1.7 任何私人药品均不得带入车间。
3.2 设备、环境
3.2.1 厂房的选址、设计、布局、建造、改造和维护必须符合药品生产要求,应当能够最大限度地避免污染、交叉污染、混淆和差错,便于清洁、操作和维护。
3.2.2 应当根据厂房及生产防护措施综合考虑选址,厂房所处的环境应当能够最大限度地降低物料或产品遭受污染的风险。
3.2.3应当有整洁的生产环境;厂区的地面、路面及运输等不应当对药品的生产造成污染;生产、行政、生活和辅助区的总体布局应当合理,不得互相妨碍;厂区和厂房内的人、物流走向应当合理。
3.2.4 厂房、设施的设计和安装应当能够有效防止昆虫或其它动物进入。应当采取必要的措施,避免所使用的灭鼠药、杀虫剂、烟熏剂等对设备、物料、产品造成污染。
3.2.5 为降低污染和交叉污染的风险,厂房、生产设施和设备应当根据所生产药品的特
性、工艺流程及相应洁净度级别要求合理设计、布局和使用,并符合下列要求:(一)应当综合考虑药品的特性、工艺和预定用途等因素,确定厂房、生产设施和设备多产品共用的可行性,并有相应评估报告;
(二)生产特殊性质的药品,如高致敏性药品(如青霉素类)或生物制品(如卡介苗或其他用活性微生物制备而成的药品),必须采用专用和独立的厂房、生产设施和设备。青霉素类药品产尘量大的操作区域应当保持相对负压,排至室外的废气应当经过净化处理并符合要求,排风口应当远离其他空气净化系统的进风口;
(三)生产β-内酰胺结构类药品、性激素类避孕药品必须使用专用设施(如独立的空气净化系统)和设备,并与其他药品生产区严格分开;
(四)用于上述第(二)、(三)项的空气净化系统,其排风应当经过净化处理;
(五)药品生产厂房不得用于生产对药品质量有不利影响的非药用产品。
3.2.6 生产区和贮存区应当有足够的空间,确保有序地存放设备、物料、中间产品、待包装产品和成品,避免不同产品或物料的混淆、交叉污染,避免生产或质量控制操作发生遗漏或差错。
3.2.7 制剂的原辅料称量通常应当在专门设计的称量室内进行。产尘操作间(如干燥物料或产品的取样、称量、混合、包装等操作间)应当保持相对负压或采取专门的措施,防止粉尘扩散、避免交叉污染并便于清洁。
3.2.8 用于药品包装的厂房或区域应当合理设计和布局,以避免混淆或交叉污染。如同一区域内有数条包装线,应当有隔离措施。
3.2.9 通常应当有单独的物料取样区。取样区的空气洁净度级别应当与生产要求一致。如在其他区域或采用其他方式取样,应当能够防止污染或交叉污染。
3.2.10 实验室的设计应当确保其适用于预定的用途,并能够避免混淆和交叉污染,应当有足够的区域用于样品处置、留样和稳定性考察样品的存放以及记录的保存。
3.2.11 设备所用的润滑剂、冷却剂等不得对药品或容器造成污染,应当尽可能使用食用级或级别相当的润滑剂。应当选择适当的清洗剂清洁设备,并防止这类设备成为污染源。
3.2.12 生产设备应易于清洁。设备中应尽量避免出现凹槽等难清洁部位。使用结束后必须将产品及包装材料从设备上清理出去,并按规定程序进行清洁、清洗、灭菌。
3.3 物料
3.3.1应当建立物料和产品的操作规程,确保物料和产品的正确接收、贮存、发放、使用和发运,防止污染、交叉污染、混淆和差错。