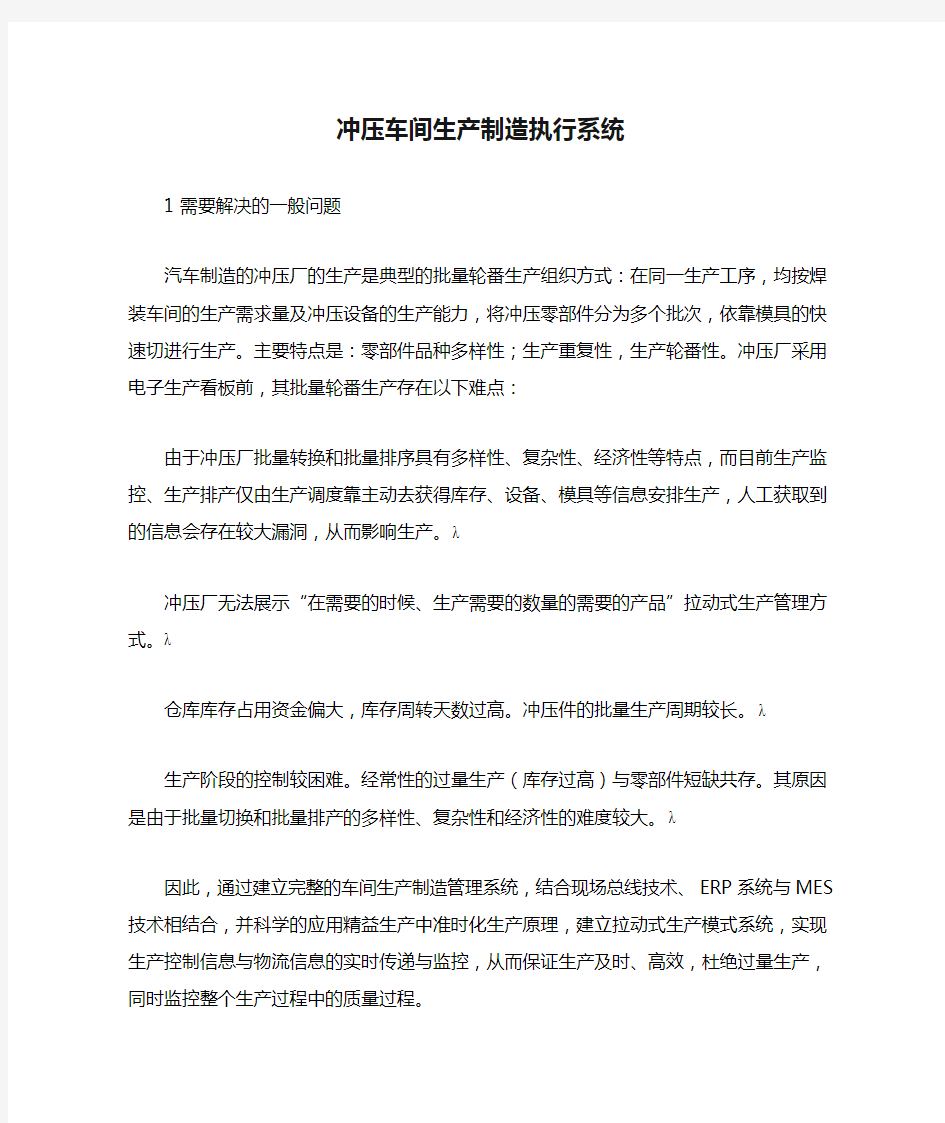
冲压车间生产制造执行系统
- 格式:doc
- 大小:22.00 KB
- 文档页数:2
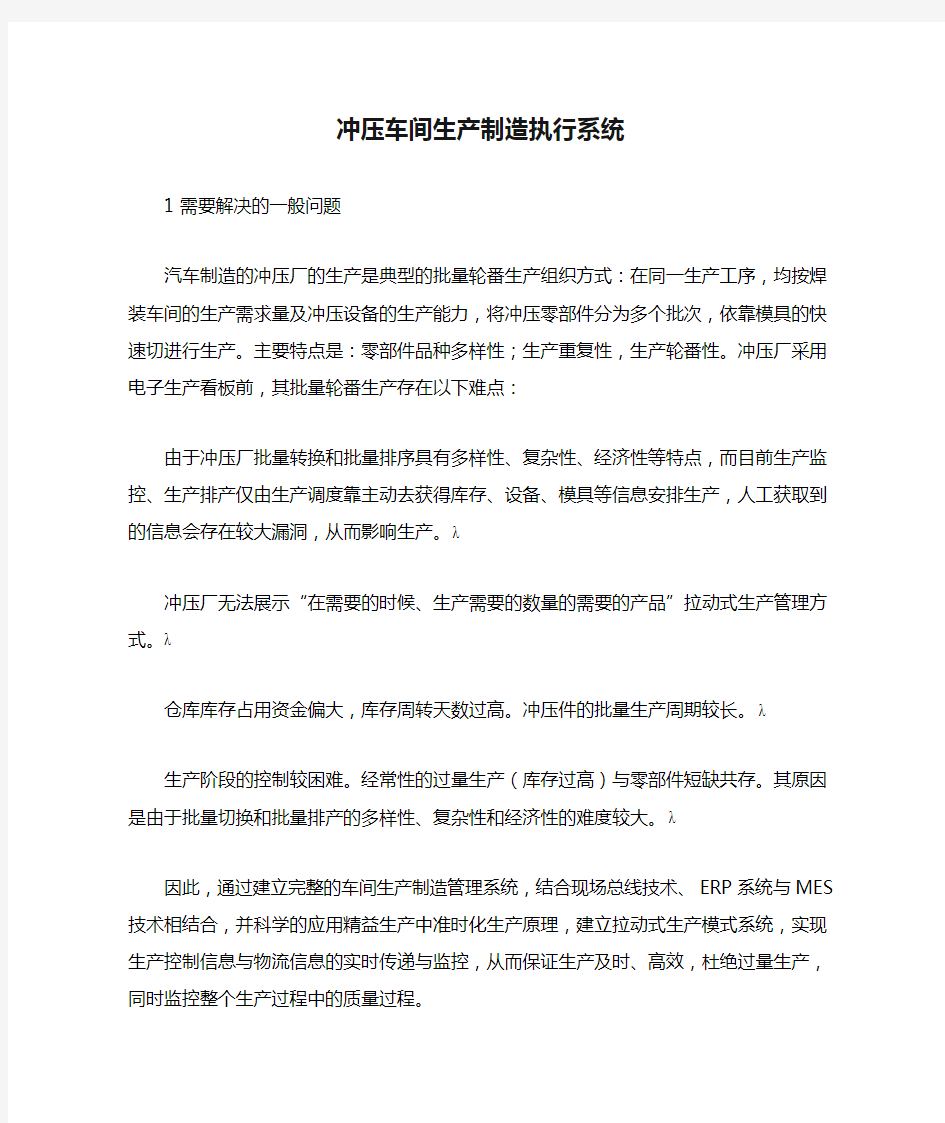
冲压车间生产制造执行系统
1 需要解决的一般问题
汽车制造的冲压厂的生产是典型的批量轮番生产组织方式:在同一生产工序,均按焊装车间的生产需求量及冲压设备的生产能力,将冲压零部件分为多个批次,依靠模具的快速切进行生产。主要特点是:零部件品种多样性;生产重复性,生产轮番性。冲压厂采用电子生产看板前,其批量轮番生产存在以下难点:由于冲压厂批量转换和批量排序具有多样性、复杂性、经济性等特点,而目前生产监控、生产排产仅由生产调度靠主动去获得库存、设备、模具等信息安排生产,人工获取到的信息会存在较大漏洞,从而影响生产。λ
冲压厂无法展示“在需要的时候、生产需要的数量的需要的产品”拉动式生产管理方式。λ
仓库库存占用资金偏大,库存周转天数过高。冲压件的批量生产周期较长。λ
生产阶段的控制较困难。经常性的过量生产(库存过高)与零部件短缺共存。其原因是由于批量切换和批量排产的多样性、复杂性和经济性的难度较大。λ
因此,通过建立完整的车间生产制造管理系统,结合现场总线技术、ERP系统与MES技术相结合,并科学的应用精益生产中准时化生产原理,建立拉动式生产模式系统,实现生产控制信息与物流信息的实时传递与监控,从而保证生产及时、高效,杜绝过量生产,同时监控整个生产过程中的质量过程。
2.冲压车间生产制造执行系统(MES)功能
系统在冲压车间主要从以下几个方面进行管理和控制:
2.1 生产计划管理
冲压车间生产计划主要以冲压件BOM表和材料定额为基础,根据汽车生产计划和冲压件要货计划,编制冲压件生产计划。
2.2 批次管理:
记录每一个生产批的批号、生产的冲压件名称、适合车型、批量、生产设备、模具、班次、班别、原材料供应商及供货批次等信息。
2.3 质量管理与监控:
2.3.1 监控的主要内容有:
缺陷:记录破裂、起皱、回弹、扭曲、划伤等缺陷,包括检查类型(专、自、互、首检)、缺陷名称、位置、严重程度、所属批次、加工设备、模具、发生岗位、发现岗位、责任部门等内容,并进行监控,发生下列情况时(可定制)自动进行报警:
单项缺陷率超过设定值λ
累计缺陷数超过设定值(通常从某一班次开始时进行计算和监控)λ
严重缺陷λ
检查人员认为需要报警的其他情况λ
精度:记录抽检的冲压件的尺寸、形状和位置精度,利用SPC进行实时监控,发现异常及时报警
性能:力学检查、探伤等结果管理
设备工艺参数:记录设备在各个作业步骤的压力、时间等工艺参数,利用SPC进行实时监控,发现异常及时报警。
冲压车间联网的作用是对整个车间的生产进行集中监控,管理;对故障进行统一的处理和记录,大幅度提高设备的生产效率,是提高产量的基础。
异常的处理:
收到报警通知后,相关责任单位进行处理,并记录处理结果。利用质量分析工具对以上内容进行深入分析,比如:
通过相关分析了解工艺参数对质量的影响λ
通过柏拉图了解多发缺陷λ
2.3.2 自动生成质量报表
2.3.3 产品追溯(质量追溯和批次追溯)
2.4 返修管理:
对本车间发现及焊装车间退回的缺陷冲压件进行返修管理
1) 记录缺陷冲压件名称、批次、发现单位、现象、原因、采取措施、工时
2) 确认:对返修件进行确认,确保不良品不流入下一环节
3) 进行知识库维护
4) 分类统计汇总分析:
缺陷及原因分类汇总排序λ
责任单位(开卷、冲压x区等)分类汇总λ
发现单位(开卷、冲压x区、测量、焊装、涂装、总装、整车品质等)分类汇总λ趋势分析λ