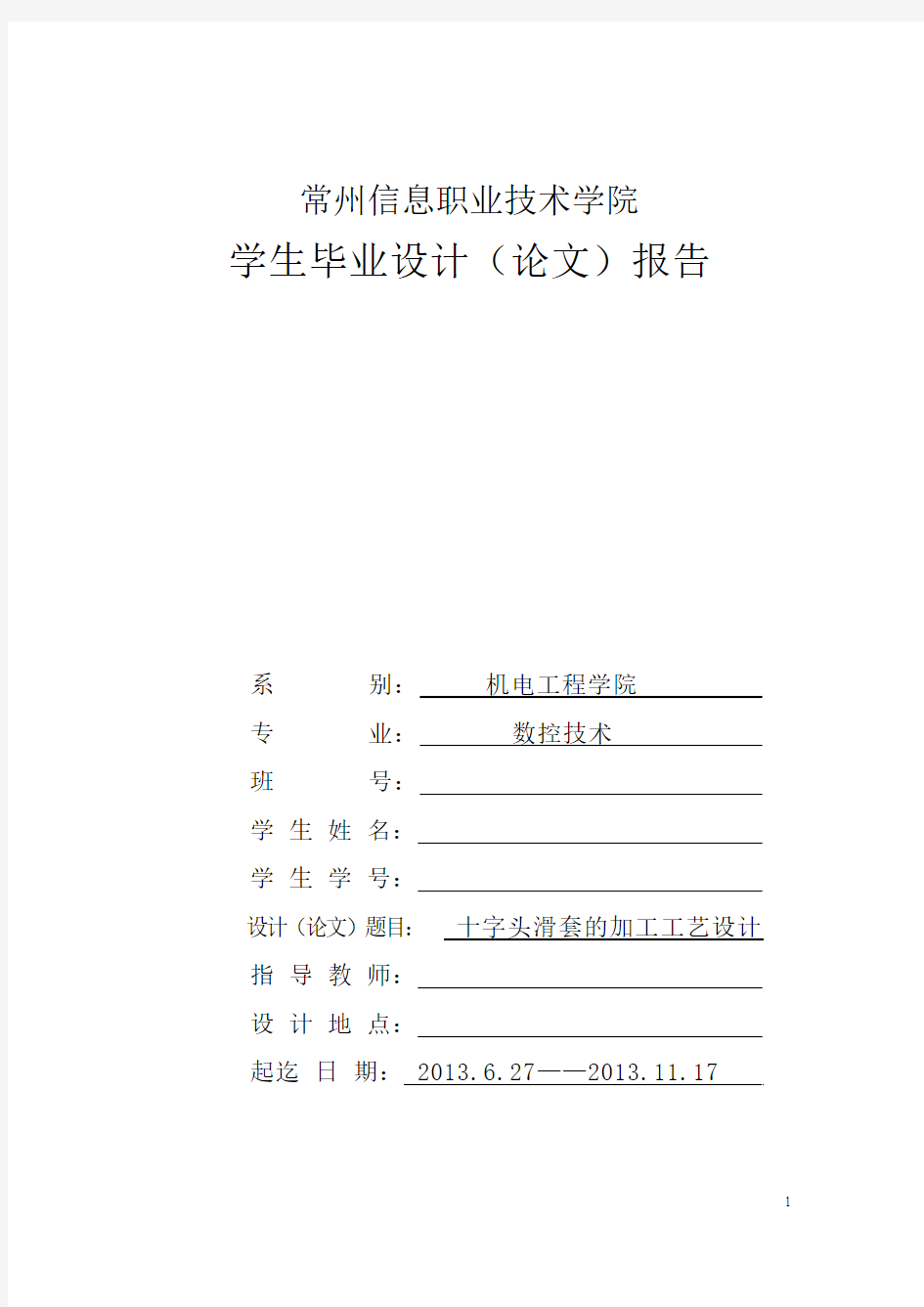
十字头滑套的加工工艺设计
- 格式:doc
- 大小:926.00 KB
- 文档页数:27
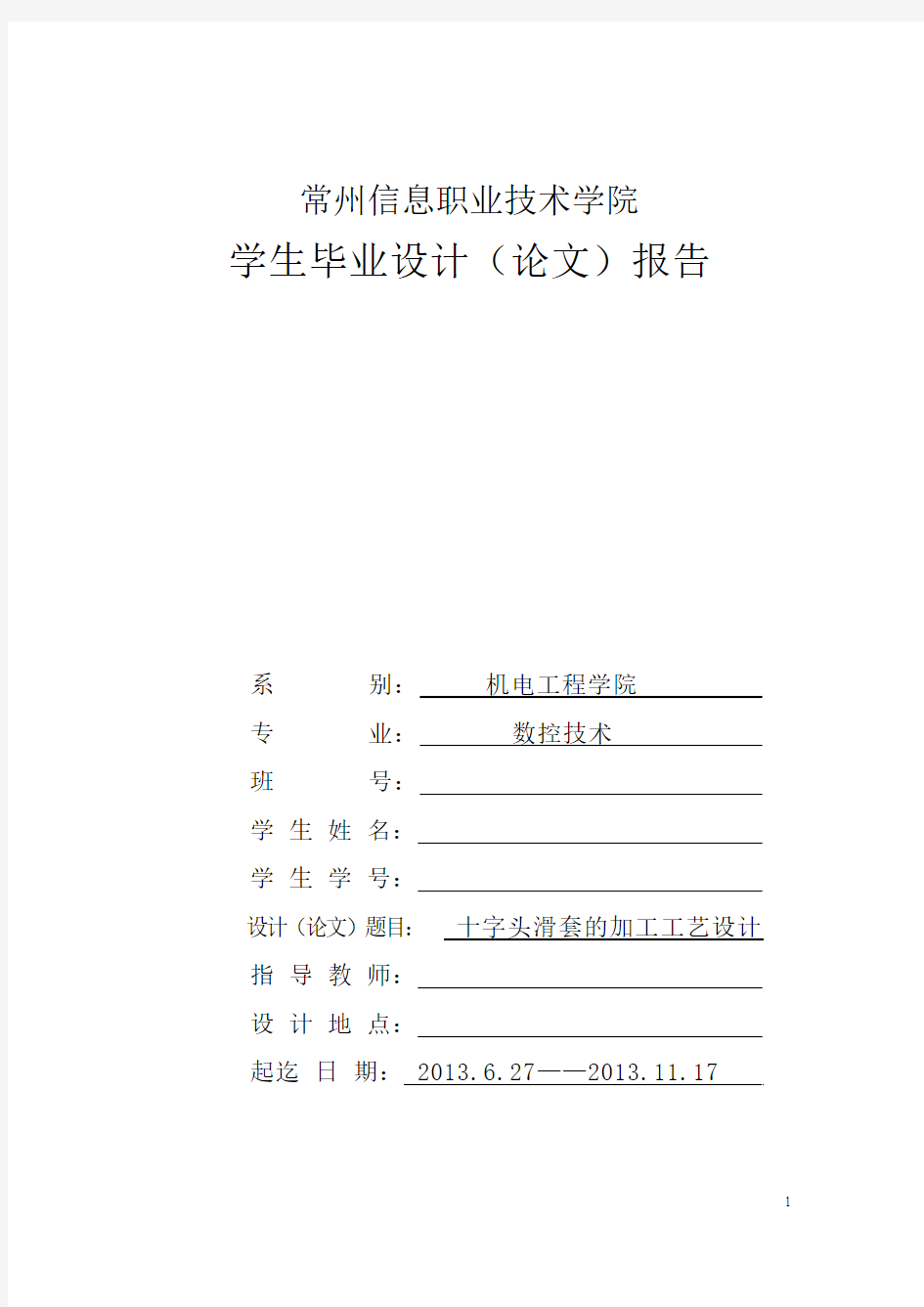
常州信息职业技术学院
学生毕业设计(论文)报告
系别:机电工程学院
专业:数控技术
班号:
学生姓名:
学生学号:
设计(论文)题目:十字头滑套的加工工艺设计指导教师:
设计地点:
起迄日期: 2013.6.27——2013.11.17
毕业设计(论文)任务书
专业数控技术班级数控113 姓名
一、课题名称:十字头滑套的加工工艺设计
二、主要技术指标:以Ф180mm孔为中心孔的加工表面,这组加工表面包括:Ф180mm内孔加工面和Ф190mm的止口加工件及其倒角,尺寸为Ф190止口与Ф180的孔的同轴度误差很高,为了保证加工精度。要以止口定位加工孔。
与Ф320mm和Ф190mmd的断面没有严格的公差要求。可以不着重考虑,上下两个215x140的面没有什么要求,见光即可。
三、工作内容和要求: 1. 填写设计任务书。
2. 撰写毕业设计开题报告,拟定设计方案。
3.制定十字滑套的加工工艺,设计8—M6的钻床夹具。
4. 中批量生产,选用通用设备。
5. 编制设计说明书,要求打印稿一份。
四、主要参考文献:____________ 1).机械设计手册。
2).机械加工工艺设计手册。
3).机床夹具设计手册。
4).机械制图手册。
5).其他相关资料___
学生(签名)年月日
指导教师(签名)年月日
教研室主任(签名)年月日
毕业设计(论文)开题报告
目录
内容摘要
前言
1零件的分析 (6)
2工艺规程设计 (7)
2.1确定毛坯的制造形式 (7)
2.2基面的选择 (7)
2.3制定工艺路线 (7)
2.4机械加工余量、工序尺寸
及毛坯尺寸的确定 (8)
2.5确定切削用量及基本工时 (8)
3专用夹具的选择 (20)
4机床及刀具的选择 (21)
5数控编程 (22)
6致谢与总结 (25)
7参考文献 (27)
1 零件的分析
零件的工艺分析
这个零件从零件图上可以看出,它一共有3组加工表面,而这三组加工表面之间有一定的位置要求,现将这二组加工表面分述如下:
1.1 以Φ180mm孔为中心的加工表面。这组加工表面包括:Φ180mm的内孔加工面和Φ190的止口加工件及其倒角,尺寸为Φ190止口和Φ180mm的孔的同轴度误差很高,为了保证加工精度。要以止口定位加工孔。
1.2与Φ320mm和Φ190mm的断面没有严格的公差要求,可以不着重考虑,上下两个215x140的面没有什么要求,见光即可。
2、工艺规程设计
2.1 确定毛坯的制造形式
零件材料为HT200,考虑到该零件在车床中受的力并保证零件的工作可靠性,零件为中批生产,而且零件的尺寸不大,因此,毛坯可以采用金属磨砂型制造。
2.2基面的选择
基准面选择是工艺规程设计中重要工作之一。基面选择的正确与合理,可以使加工质量得到保证,生产效率得以提高。否则,加工工艺过程中会问题百出,更有甚者,还会造成零件大批报废,使生产无法正常进行。
粗基准的选择:以上下表面和两侧面作为粗基准,以消除Z向,X向,Y向三个自由度,达到完全定位。
对于精基准而言,根据基准重合原则,选用设计基准作为精基准。
2.3制定工艺路线
制定工艺路线的出发点,应当是使零件的几何形状得到合理的保证。在生产纲领中为中批量生产的条件下,可以考虑采用万能性机床配以专用夹具来提高生产率。除此以外,还应当考虑经济效率,以便使生产成本尽量下降。
1、工艺路线方案一
工序Ⅰ铸造。
工序Ⅱ时效处理。
工序Ⅲ平Φ335端面,见光。
工序Ⅳ平另一端面。
工序Ⅴ铣上平面。
工序Ⅵ铣下平面。
工序Ⅶ钻上平面孔。
工序Ⅷ钻下平面孔。
工序Ⅸ以下平面和端面定位镗Φ180的孔和Φ190的止口。
工序Ⅹ镗Φ190偏差为-0.1的外圆。
工序Ⅺ钻Φ335面上的14-Φ22孔。
工序Ⅻ钻Φ320面上的14-Φ22的孔。
工序Ⅻⅰ去毛刺。
工序ⅩⅢ质检,入库。
2、工艺路线方案二
工序Ⅰ铸造。
工序Ⅱ时效处理。
工序Ⅲ平Φ335端面,见光。
工序Ⅳ平另一端面。
工序Ⅴ铣上平面。
工序Ⅵ铣下平面。
工序Ⅶ钻上平面孔。
工序Ⅷ钻下平面孔。
工序Ⅸ以下平面和端面定位镗Φ180的孔和Φ190的止口。
工序Ⅹ镗Φ190偏差为-0.1的外圆。
工序Ⅺ钻Φ335面上的14-Φ22孔。
工序Ⅻ钻Φ320面上的14-Φ22的孔。
工序ⅹⅡⅰ去贸促
工序ⅩⅡⅡ质检,入库。
工艺方案的比较与分析
上述两个工艺方案的特点在于:方案一是先山下面,再以下面为基准镗孔。方案二是先镗孔在加工上下表面。两相比较可以看出,方案一可以避免加工上定位基准和设计基准不重合的问题,从而保证了止口和内孔的同轴度,而方案二不能,所以选用方案一作为零件的加工工序。
2.4机械加工余量、工序尺寸及毛坯尺寸的确定
“拔叉”零件材料为HT200,毛坯重量约为54Kg,生产类型为中批量生产。采用金属磨砂铸造。
根据上述原始资料及加工工艺,分别确定各加工表面的机械加工余量、工序尺寸及毛坯尺寸如下:
1.铣端面
考虑左端面的粗糙度Ra为 3.2,参照《机械制造工艺设计手册》——一以下简称“手册”,表1—43,确定工序尺寸为Z=3.0mm,其中粗加
工的加工余量Z=2.0mm,精加工余量Z=1.0mm,右端面没有粗精度要求,
只要求粗加工,所以余量定位3.0mm
2.铣表面
根据“手册”表1—49,取上表面的机械加工余量为 4.0mm,下表面
的余量为3.0mm.
粗铣上表面 Z=3.0mm
精铣上表面的台阶面 Z=1.0mm
粗铣下表面 Z=3.0mm
2.5确定切削用量及基本工时
工序Ⅰ:铣端面
1\粗铣直径为335端面
a(f)=0.25mm/Z
v=0.35m/s (21m/min)