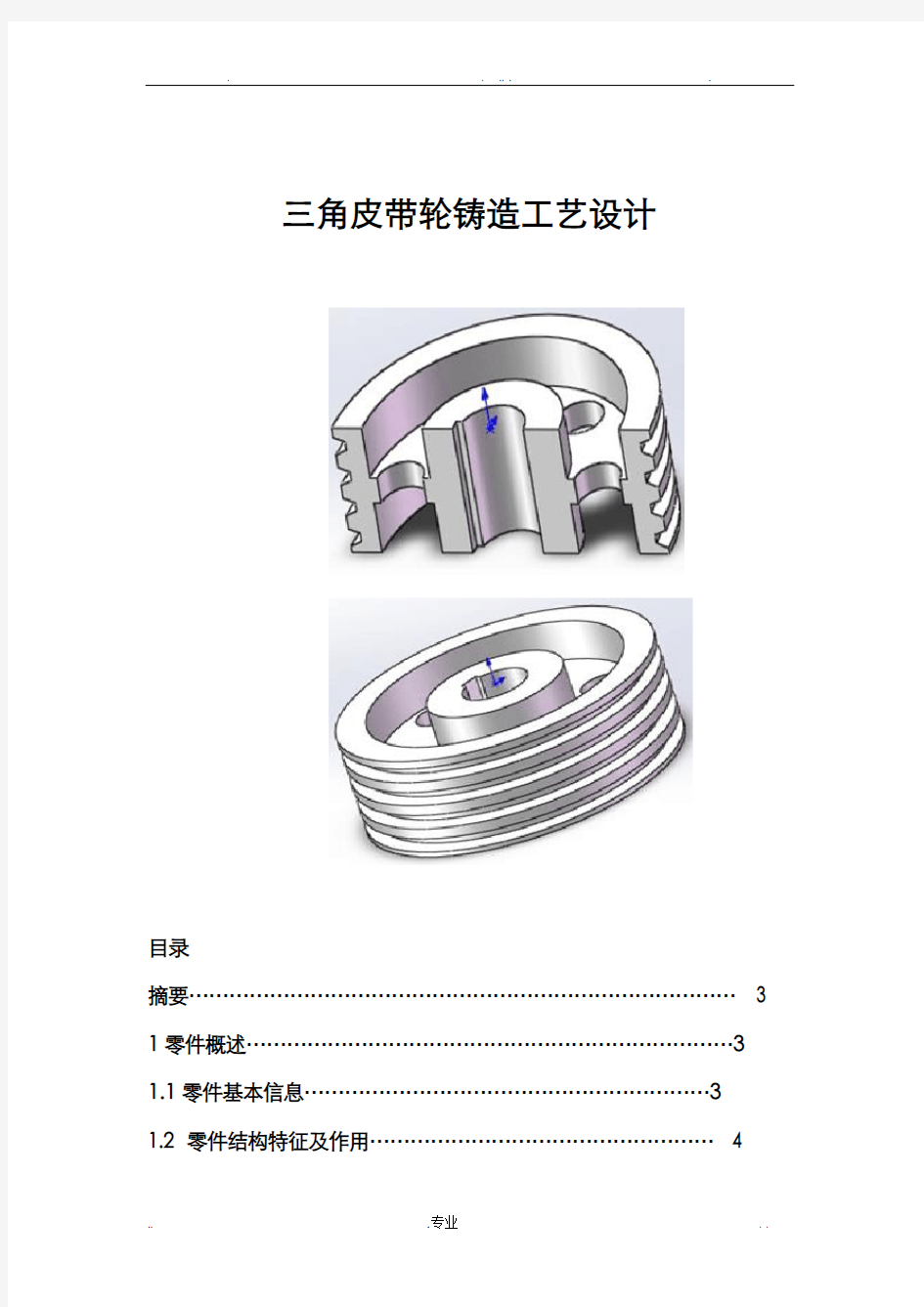
三角皮带轮铸造工艺设计
- 格式:doc
- 大小:700.50 KB
- 文档页数:23
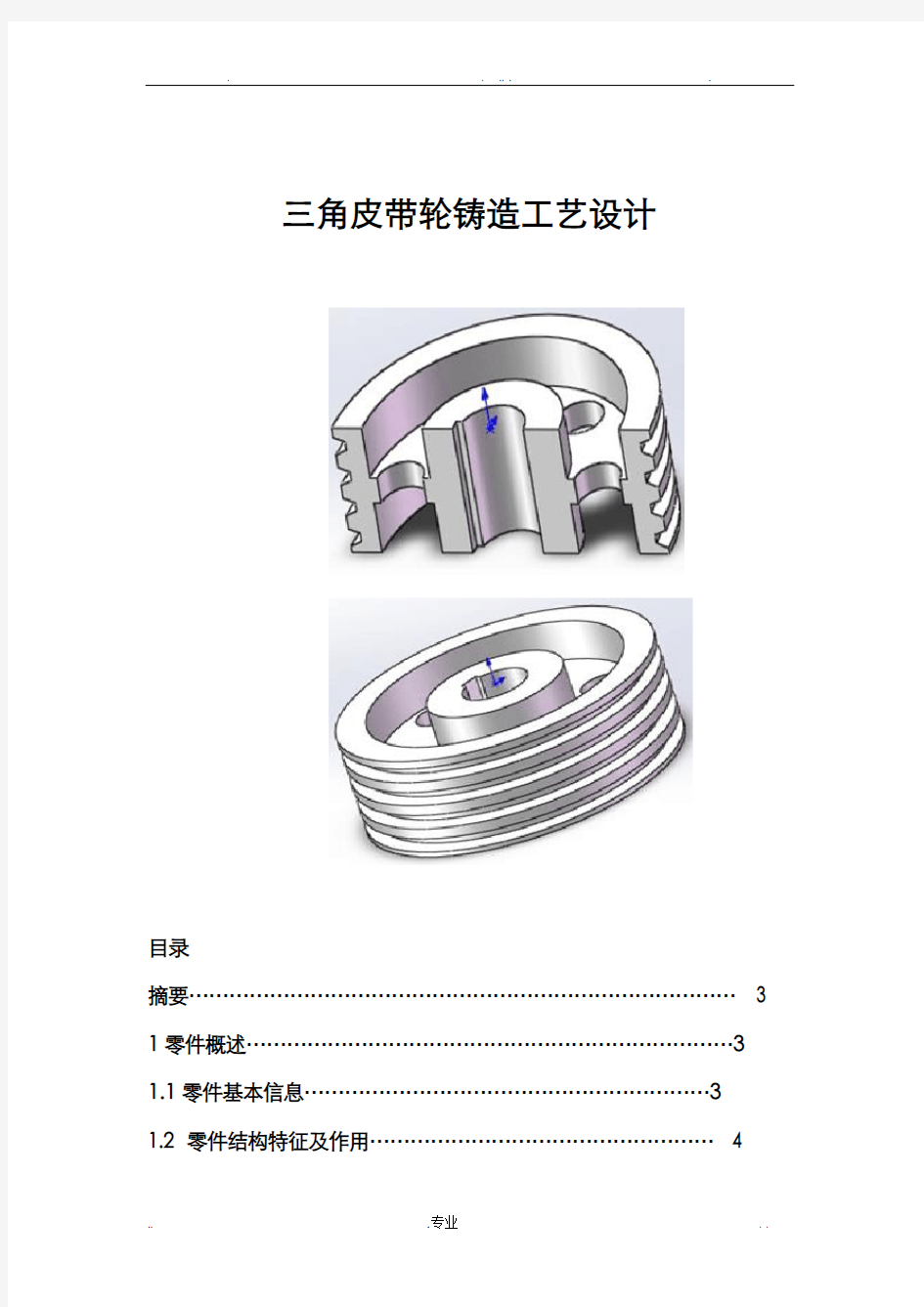
三角皮带轮铸造工艺设计
目录
摘要 (3)
1零件概述 (3)
1.1零件基本信息 (3)
1.2 零件结构特征及作用 (4)
1.3 零件结构审查 (4)
1.4 零件技术要求 (5)
2 铸造工艺方案设计 (5)
2.1 造型、造芯材料及方法 (5)
2.2 浇注位置的确定 (6)
2.3 分型面的选择 (7)
2.4 砂芯设计 (8)
2.5 铸造工艺设计参数 (11)
3 浇注系统 (15)
3.1 浇注系统类型选择 (15)
3.2 浇注系统结构设计 (15)
3.3 浇口位置及数量的确定 (15)
3.4 浇注系统尺寸计算 (16)
3.5 浇注系统各单元结构及尺寸 (17)
4. 冒口的设计 (19)
5冷铁的设计 (20)
5.1冷铁放置位置的确定 (20)
5.2冷铁尺寸的确定 (21)
5.3设计冷铁时注意事项 (21)
6 出气孔的设计 (22)
参考文献 (22)
摘要
皮带轮是带传动结构重要的零件之一,相比较传统汽车乘用车发动机减震皮带轮,轻型柴油乘用车发动机减震皮带轮既可满足家用轿车发动机上,又可适用大型客车,大型货车,农用车上的发动机上,具有回收循环使用、重量轻、增强发动机的动力、降低油耗等优点。本文依照铸造工艺设计的一般程序对三角带轮进行了分析,从技术条件和结构着手,参考有关铸造手册和分析相关实例,确定了合理的铸造工艺方案,最终完成了其铸造工艺设计,这为我们今后设计铸造工艺奠定了理论和实践基础。
1 零件概述
1.1 零件基本信息
零件名称:三角皮带轮
零件材料:QT450-10
产品生产纲领:大批量生产
砂箱高度:250
三角带轮零件图:
图1 三角带轮零件图
1.2 零件结构特征及作用
本三角皮带轮采用腹板式结构,结构简单,且是左右上下对称的回转体,易于分型和铸造,大大提高生产效率,重复率高。
1.3 零件结构审查
审查、分析铸件结构时应考虑以下几个方面:
(1)铸件应有合适的壁厚,为了避免浇不到、冷隔等缺陷铸件不应太薄。
(2)铸件结构不应造成严重的收缩阻碍,注意壁厚过渡和圆角。
(3)铸件壁应薄于外壁。
(4)壁厚力求均匀,减少肥厚部分,防止形成热节。
(5)利于补缩和实现顺序凝固。
(6)防止铸件翘曲变形。
(7)避免浇注位置上有水平的大平面结构。
三角皮带轮零件轮廓尺寸为290mm*290mm*90mm,由《铸造
工艺学》表2-1,知:砂型铸造时球墨铸铁铸件最小允许壁厚为4~8mm。而三角皮带轮的最小壁厚为11mm,符合要求。1.4 零件技术要求
铸造圆角R5,铸造斜度1:20,所有倒角2×45°,铸件除满足几何尺寸精度和材质要求外,没有其它的特殊要求。
2 铸造工艺方案设计
2.1 造型、造芯材料及方法
零件轮廓尺寸为290mm*290mm*90mm,尺寸较小,属于中小型零件且需要大批量生产。采用湿型粘土砂造型灵活性大,生产率高,生产周期短,便于组织流水生产,易于实现机械化和自动化,材料成本低,节省烘干设备、燃料、电力等,还可延长砂箱使用寿命。因此,采用湿型粘土砂机器造型,模样采用金属模是合理的。
在造芯材料及方法选择中,如用粘土砂制作砂芯原料成本较低,但是烘干后容易产生裂纹,容易变形。在大批量生产的条件下,由于
需要提高造芯效率,且常要求砂芯具有高的尺寸精度,此工艺所需的砂芯采用热芯盒法生产砂芯,以增加其强度及保证铸件质量。选择使用射芯工艺生产砂芯,采用热芯盒制芯工艺热芯盒法制芯,是用液态固性树脂粘结剂和催化剂制成的一种芯砂,填入加热到一定的芯盒,贴近芯盒表面的砂芯受热,其粘结剂在很短的时间硬化。而且只要砂芯表层有数毫米的硬壳即可自芯取出,中心部分的砂芯利用余热可自行硬化。
2.2 浇注位置的确定
铸件的浇注位置是浇注状态下铸件在铸型所处的位置。确定浇注位置是铸造工艺设计中重要的环节,关系到铸件的在质量、铸件的尺寸精度及造型工艺过程的难易程度。确定浇注位置时应注意以下几个原则:
(1)铸件重要部分或主要加工面、耐磨面、受力部位等应位于下部或呈直立状态;
(2)铸件局部薄壁部位或铸件大平面应朝下;
(3)有利于铸件顺序凝固和补缩;
(4)尽可能避免用吊砂、吊芯或悬壁式砂芯;
(5)通常使合型位置、浇注位置和铸件冷却位置一致。
基于以上原则,铸件浇注位置如图2所示:
图2 三角带轮的浇注位置
2.3 分型面的选择
分型面是指两半铸型相互接触的表面。分型面的优劣在很大程度上影响铸件的尺寸精度、成本和生产率。
一般来说,选择分型面时应注意一下原则:
1.应使铸件全部或大部分置于同一半型
2.应尽量减少分型面的数目
3.分型面应尽量选用平面
4.便于下芯、合箱和检测
5.不使砂箱过高
6.受力件的分型面的选择不应削弱铸件结构强度
7.注意减轻铸件清理和机械加工量
2.4 砂芯设计
砂芯用来形成铸件腔或外形上有碍起模的局部凸凹部位。设计砂芯总的原则是:铸件腔尺寸准确、通气顺畅、芯盒结构简单。
2.4.1 芯头的设计
砂芯主要靠芯头固定在砂型上。对于垂直芯头为了保证其轴线垂直、牢固地固定在砂型上,必须有足够的芯头尺寸。
垂直芯头的设计数据包括上、下芯头高度和芯头斜度、芯头间隙、上部压紧环与下部集砂槽等。详细数据可查标准JB/T5106-1991。
1.芯头高度
对于φ60mm的孔,L=90mm,D=60mm,查《铸造工艺学》表6-17知,芯头高度h=25~30mm,取h=30mm。因为带轮的垂直砂芯是上、下对称的,且产品是大量生产的,故上、下芯头可采用相同的高度。
对于φ42mm×6均匀分布的孔,L=18mm,D=42mm,查表6-17知,芯头高度h=15~20mm,取h=20mm。
2.芯头斜度
为避免合型时上芯头和铸型相碰,上芯头和上芯座的应大一些。查《铸造工艺学》表6-18知,上芯头α=10º,下芯头α=5º。
3.芯头与芯座间的间隙
机器造型时,制芯时间隙一般较小,常用间隙为0.5mm~1mm。
4.压紧环
湿型铸造时,为阻止金属液沿间隙钻入芯头堵塞通气孔,应在上芯座上安置一圈凸起的砂环,称为压紧环。合型后它能将砂芯压紧,能有效阻止金属液钻入芯头中心通气道中。
5.集砂槽