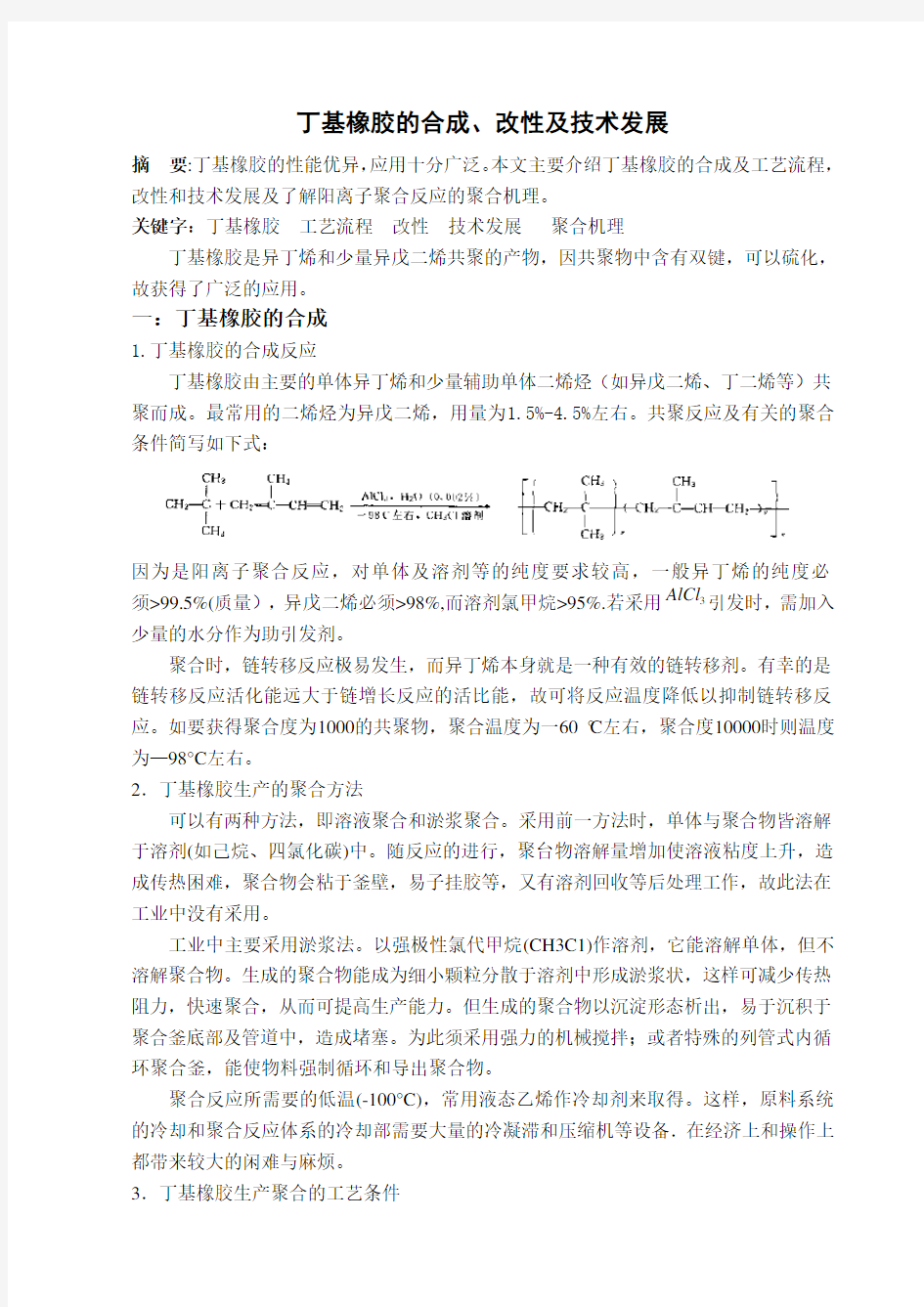
丁基橡胶的合成
- 格式:doc
- 大小:213.08 KB
- 文档页数:9
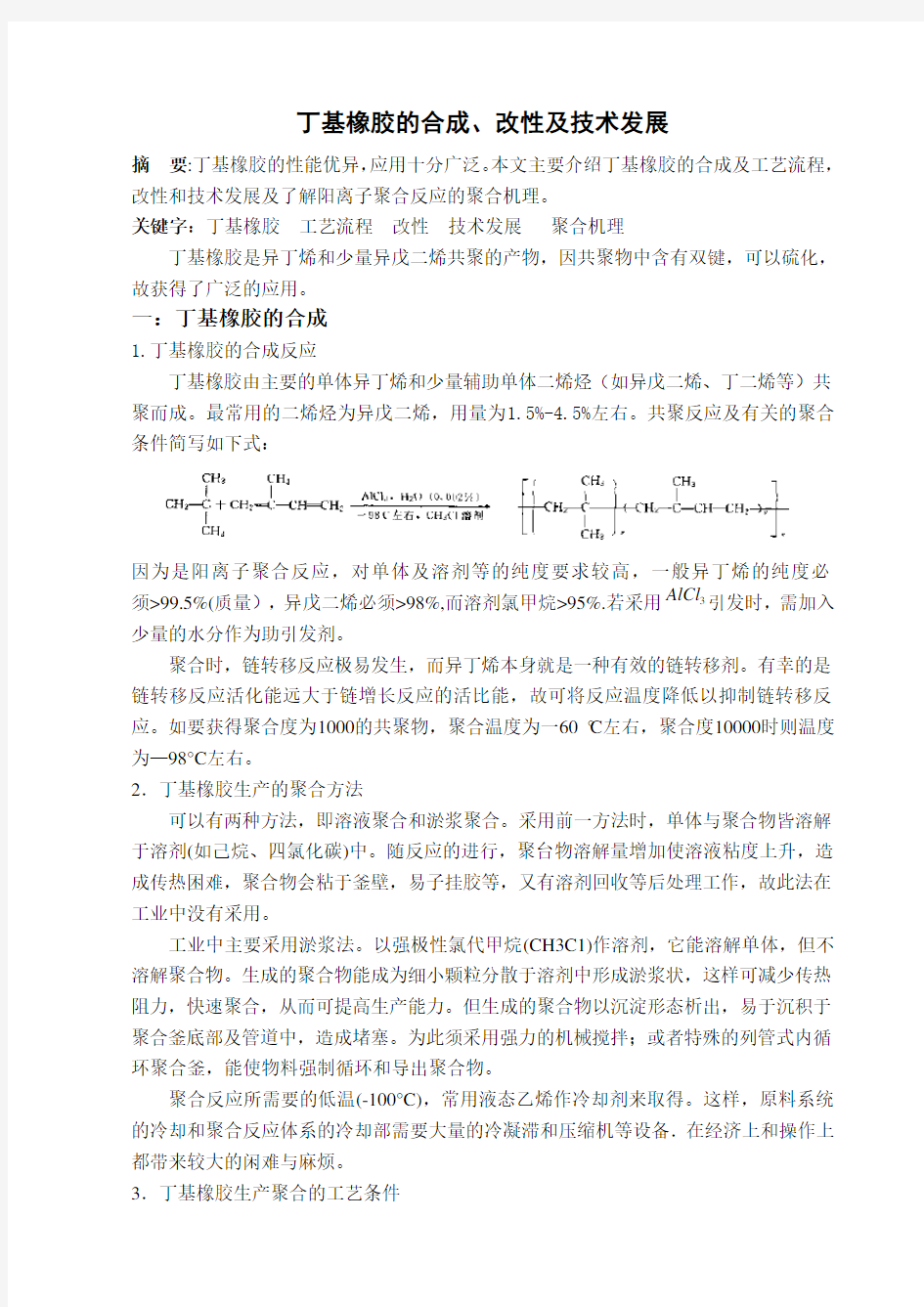
丁基橡胶的合成、改性及技术发展
摘要:丁基橡胶的性能优异,应用十分广泛。本文主要介绍丁基橡胶的合成及工艺流程,
改性和技术发展及了解阳离子聚合反应的聚合机理。
关键字:丁基橡胶工艺流程改性技术发展聚合机理
丁基橡胶是异丁烯和少量异戊二烯共聚的产物,因共聚物中含有双键,可以硫化,
故获得了广泛的应用。
一:丁基橡胶的合成
1.丁基橡胶的合成反应
丁基橡胶由主要的单体异丁烯和少量辅助单体二烯烃(如异戊二烯、丁二烯等)共
聚而成。最常用的二烯烃为异戊二烯,用量为1.5%-4.5%左右。共聚反应及有关的聚合
条件简写如下式:
因为是阳离子聚合反应,对单体及溶剂等的纯度要求较高,一般异丁烯的纯度必
AlCl引发时,需加入须>99.5%(质量),异戊二烯必须>98%,而溶剂氯甲烷>95%.若采用3
少量的水分作为助引发剂。
聚合时,链转移反应极易发生,而异丁烯本身就是一种有效的链转移剂。有幸的是
链转移反应活化能远大于链增长反应的活比能,故可将反应温度降低以抑制链转移反
应。如要获得聚合度为1000的共聚物,聚合温度为一60 °C左右,聚合度10000时则温度
为—98°C左右。
2.丁基橡胶生产的聚合方法
可以有两种方法,即溶液聚合和淤浆聚合。采用前一方法时,单体与聚合物皆溶解于溶剂(如己烷、四氯化碳)中。随反应的进行,聚台物溶解量增加使溶液粘度上升,造成传热困难,聚合物会粘于釜壁,易子挂胶等,又有溶剂回收等后处理工作,故此法在工业中没有采用。
工业中主要采用淤浆法。以强极性氯代甲烷(CH3C1)作溶剂,它能溶解单体,但不溶解聚合物。生成的聚合物能成为细小颗粒分散于溶剂中形成淤浆状,这样可减少传热阻力,快速聚合,从而可提高生产能力。但生成的聚合物以沉淀形态析出,易于沉积于聚合釜底部及管道中,造成堵塞。为此须采用强力的机械搅拌;或者特殊的列管式内循环聚合釜,能使物料强制循环和导出聚合物。
聚合反应所需要的低温(-100°C),常用液态乙烯作冷却剂来取得。这样,原料系统
的冷却和聚合反应体系的冷却部需要大量的冷凝滞和压缩机等设备.在经济上和操作上
都带来较大的闲难与麻烦。
3.丁基橡胶生产聚合的工艺条件
一般丁基橡胶生产聚合的工艺条件为:
异丁烯/异戊二烯约97/3(质量)聚合温度约-100 °C
异丁烯浓度25%-40%(质量)聚合转化率:异丁烯75%-95% 溶剂氯代甲烷异戊二烯45%-85% 引发剂AlCl3 浓度0.2%-0.3% 产品丁基橡胶的不饱和度>1.55(摩尔)
4.丁基橡胶的生成工艺流过程
丁基橡胶的工业生产常采用不良溶剂的淤浆聚合法,其流程如图所示:
丁基橡胶制造过程简化流程图
1—进料混合,2—C2H4冷却器,3—NH3冷却器,5—反应器,6—闪蒸罐,7—过滤器8—脱水挤出机,9—干燥挤出机,10—打包机
将粗异丁烯和氯甲烷分别在脱水塔和精馏塔进行脱水和精制以后,与异戊二烯在混合槽忠按一定的比例混合。混合液在冷却器里冷至-100°C,然后送人反应器。同时配制好催化剂溶液并冷却。聚合反应在-98°C左右进行,几乎瞬时完成。聚合物在氯甲烷中沉淀形成颗粒状浆液。聚合后的淤浆从反应器中溢流出来进入盛有热水的闪蒸罐,在此蒸发氯甲烷和未反应单体。橡胶的水淤浆液用泵送到挤出干燥系统,干燥后包装成品。闪蒸罐出来的蒸气经活性氧化铝干燥、分馏后送到进料和催化剂配制系统循环使用。下图为丁基橡胶的工艺流程简图。
5.设备
丁基橡胶的聚合反应器是一种热交换器型的强制循环多管式聚合反应器。在中心部分有上升流体流动的筒管,而在其周围有小口径列管供下降流体用。液化乙烯从下部通入夹管在其内部蒸发达到冷却的目的,以保持聚合温度在-100°C左右。聚合时将异丁烯和异戊二烯溶于3倍体积的CH3Cl溶剂中,从反应器底部通入。同时从底部的另一管道
通入配制好的AlCl3的CH3Cl溶液。AlCl3含量约为单体含量的0.02%,共聚物从反应器的上部出料口溢出,而大部分CH3Cl则同时从周围的小口径列管回流至反应器的底部循环使用。
为防止聚合反应器内发生聚合物的沉淀与挂胶,一般要求淤浆在反应器内有2~5m/s 的流速。因此,强有力的搅拌器是这一聚合体系必不可少的。下图是丁基橡胶的反应器的结构。
二.丁基橡胶的聚合机理
丁基橡胶的聚合反应历程可分为链引发、链增长、链终止等三个步骤。
1.链引发
随着采用的催化剂的不同,阳离子的聚合催化剂的引发机理有所不同。
丁基橡胶的生产以淤浆法为主,其聚合机理是典型的阳离子聚合机理。以氯甲烷为溶剂、三氯化铝为引发剂、水位共引发剂,在-103°C低温下进行阳离子共聚合,其反应机理如下:
(1)链引发反应
(2)链增长
(3)链终止a.自发终止
b.成键终止
丁基橡胶的聚合机理特征主要是:快引发、快增长、易转移、难终止。
三.影响聚合反应的主要因素
1.杂质
在丁基橡胶的聚合体系中,有原料、惰性气体、聚合反应器、管道都可能带来杂质。按照其作用原理,这些杂质可以分为给电子体和烯烃两大类。给电子体如水、甲醇、氯化氢、二甲醚、二氧化硫和氨等,分子中均含有未共用的电子对,而催化剂AlCl3则有未排满的电子层,因而这些杂质均可与AlCl3反应生成络合物。例如甲醇与AlCl3生成络合物。
当这些杂质含量极少时,与AlCl3生成的络合物可以离解成为活性催化剂;但是,杂质与AlCl3反应生成活性不高,会导致转化率降低。因为这些杂质具有链转移作用,当他们超过一定量时,则会致使聚合物分子量明显降低。分子量降低的程度与杂质和AlCl3反应生成的化合物的离解度的大小有关;离解度越大,能够进行转移的负离子浓度越高,聚合物的分子量越小;也与杂质AlCl3络合物的浓度有关;浓度越高,分子量越小。
2.单体浓度和配料比
在丁基橡胶的聚合体系中:单体浓度过高,反应温度升高的很快,反应过于激烈难以控制,容易导致结块,甚至催化剂还未加足量价被迫停止反应。而单体浓度过低时,结冰现象严重,(CH3Cl的冰点为-97°C)也不能获得较高的转化率。
3.聚合温度
随着聚合温度的提高,聚合物的分子量直线下降。这是因为单体链转移活化能总是比链生长的活化能大17.56~19.23kJ/mol,因此低温能够抑制单体的链转移从而有利于分子量的增大。需要指出的是,降低温度也有可能提高聚合速度,有利于生成高分子量的聚异丁烯。因为催化体系的实际能力与下列平衡有关: