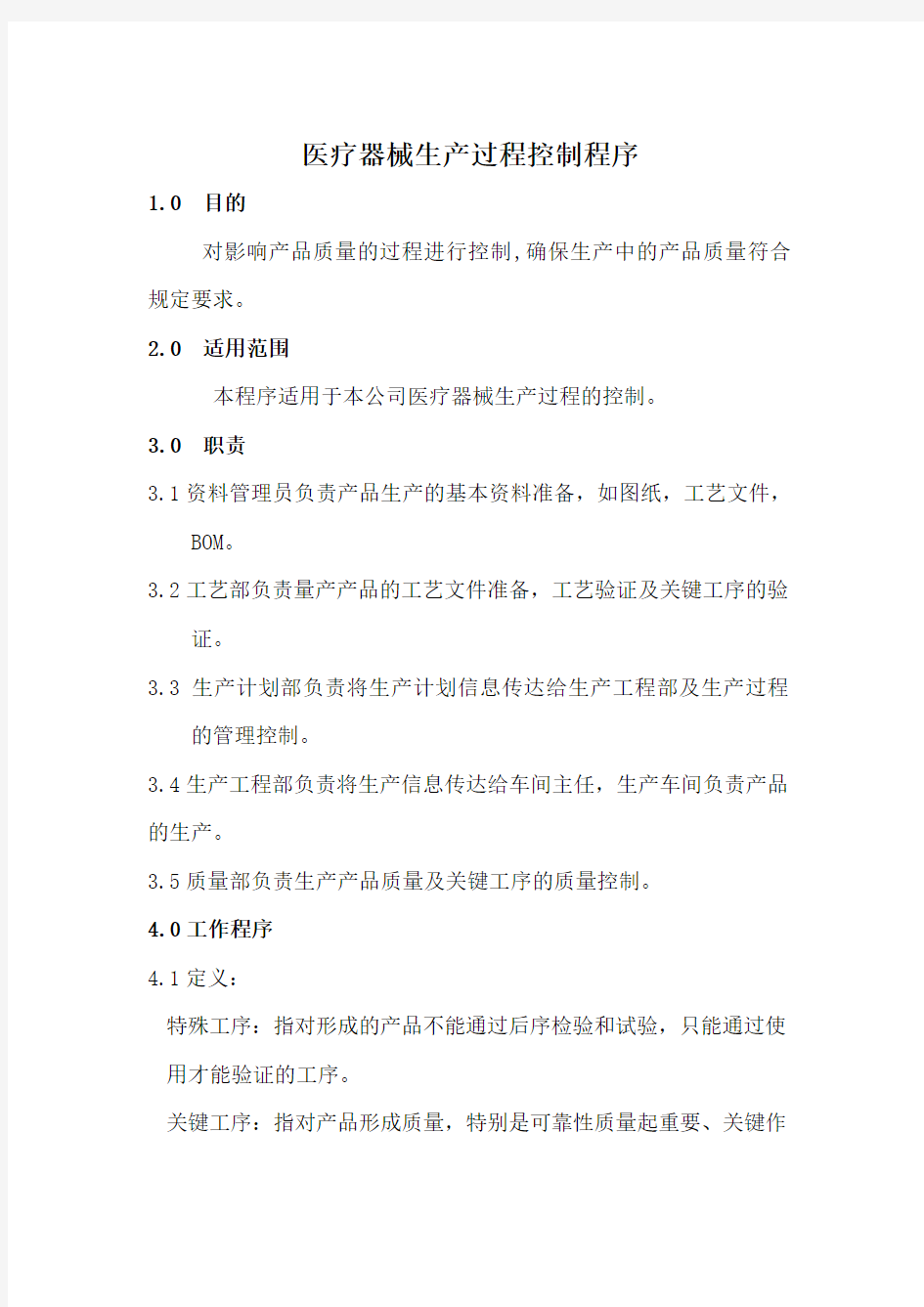
医疗器械生产过程控制程序
- 格式:doc
- 大小:34.50 KB
- 文档页数:9
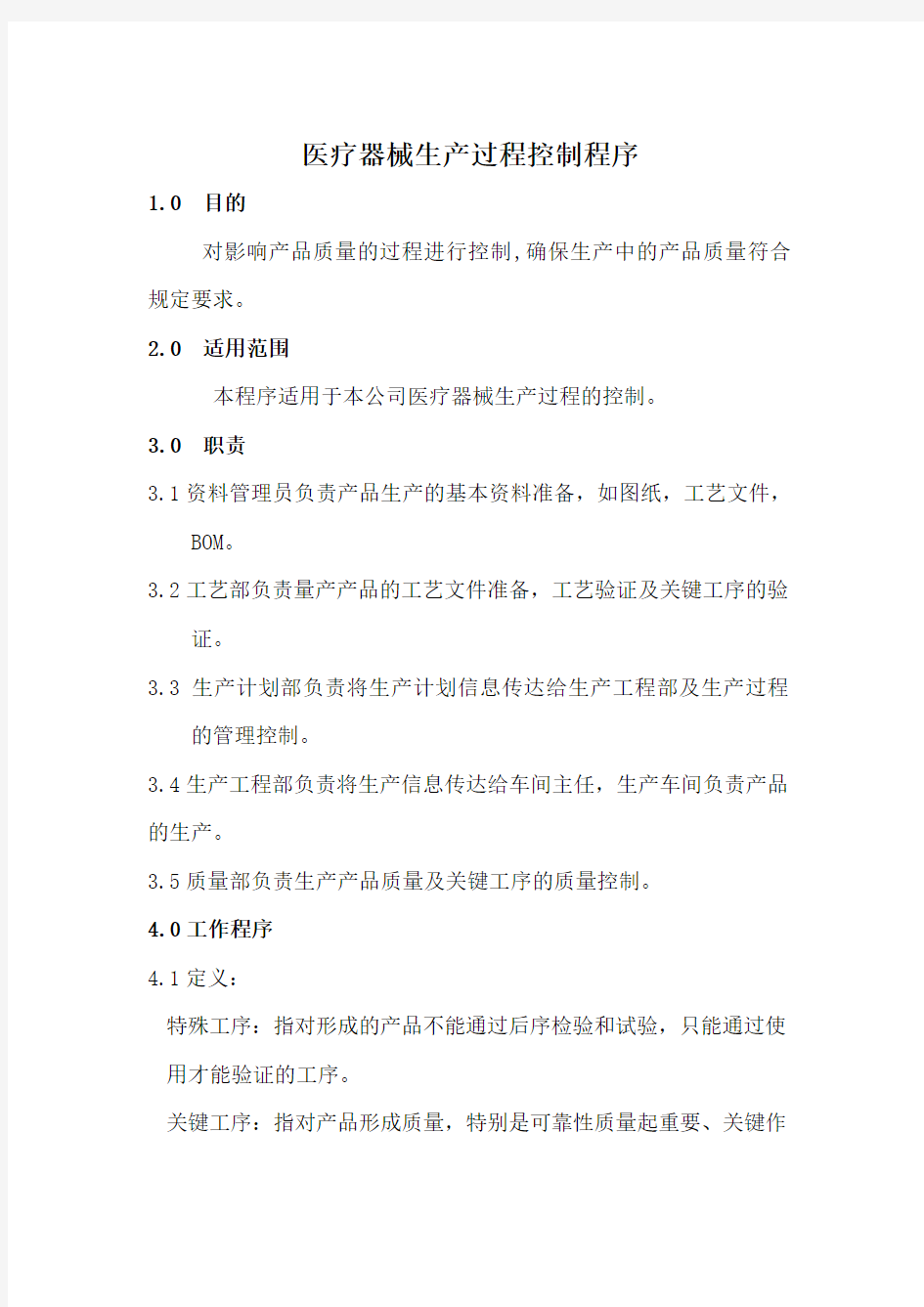
医疗器械生产过程控制程序
1.0 目的
对影响产品质量的过程进行控制,确保生产中的产品质量符合规定要求。
2.0 适用范围
本程序适用于本公司医疗器械生产过程的控制。
3.0 职责
3.1资料管理员负责产品生产的基本资料准备,如图纸,工艺文件,
BOM。
3.2工艺部负责量产产品的工艺文件准备,工艺验证及关键工序的验
证。
3.3 生产计划部负责将生产计划信息传达给生产工程部及生产过程
的管理控制。
3.4生产工程部负责将生产信息传达给车间主任,生产车间负责产品的生产。
3.5质量部负责生产产品质量及关键工序的质量控制。
4.0工作程序
4.1定义:
特殊工序:指对形成的产品不能通过后序检验和试验,只能通过使用才能验证的工序。
关键工序:指对产品形成质量,特别是可靠性质量起重要、关键作
用的工序。
4.2生产过程的控制
4.2.1 生产计划部根据《销售订单》编制《生产计划》,确保订单与
计划一致,不按照订单制作生产计划时,应经生产副总批准。生产计划完成后发放至生产车间,定期跟踪生产实际进行情况。4.2.2采购部门根据生产计划部门的编制的《____ 产品采购物资需
求表》、《___产品外协件需求表》,低值易耗品的采购按照《___月份低值易耗品及工装需求表》编制采购计划,并按计划进行采购。
4.2.3生产工程部根据生产计划安排生产,将图纸和《随工单》一起
下发给车间主任。并在《随工单》上标明加工的数量和产品编号/批号等信息及工时定额,要求工人在规定的工时内完成。
4.2.4车间主任将《随工单》及图纸安排给相应班组的班长或操作者。
4.2.5操作者的备料及工位器具的准备
4.2.
5.1操作者根据班组长安排的图纸(或者根据bom)领料,生产
性物资领料的领料按产品出库单领取,注明用于何种产品、辅助性物资领料、消耗性物资领料按其他出入库单领取,投入工序使用的原材料(零部件)、半成品必须经检验合格和批准放行后方可使用。
4.2.
5.2 生产过程中工位器具准备
1)生产中所需的生产设备、模具、模板按《设备控制程序》进行。2)生产中所需的监视和测量设备按《监视和测量设备控制程序》执
行。监视、测量和试验设备必须是校准合格的,并且在校准周期内,设备管理部门应定期对监视、测量设备进行维护、校准管理,确保测量精度和测量结果的准确性和可信性。
3)工人自己领用的工位器具由工人自己保存,出现遗失由借用者负责赔偿。
4)车间现场共同使用的工位器具,必须放置在指定位置,使用完成后重新放回指定位置。
4.2.6物料及工位器具准备齐全后,操作者按照图纸(或工艺文件)
的要求及《随工单》要求的数量进行生产。加工完成的零部件报检验员检验,检验合格后方可转入下道工序,有检验员签字的《随工单》随工序流转。
4.2.7车间在制品应以《随工单》作为追溯依据,由上一工序的操作
者将带有检验员签字的《随工单》及图纸亲自送到下道工序的
操作者或者下道工序的班组长手中,没有检验员的签字下道工
序的操作者或班组长不准接收。
4.2.8不能立即流转或不需要流转的车间在制品存放于半成品区,由
半成品保管员办理入库手续,并做好标识。
4.2.9操作者在实际生产过程中,发现图纸(工艺文件)有错误时,
按《变更控制程序》提出《变更申请》,不准自行更改。
4.2.10过程中的不合格品应明确标识,隔离放置,按《不合格品控制程序》处理。
4.2.11产品的清洁与污染控制
1)所有部件在装配前必须经过清洁处理,用洁净软布擦拭干净,产品外漏表面贴板材
护膜后方可工序流转。
2)产品装配完成后必须用工业吸尘器对箱体内部的各个角落做清洁处理,对外部表面用软棉布擦拭干净。经清洁处理后的产品无肉眼可见的污物,确保使用人员开箱后即可投入使用。清理后提交产品《请验单》,提交检验。
3)产品经检验合格后,用拉伸膜或气泡塑料薄膜对产品进行包装,可快速拆卸的部件应拆卸下单独包装。检验员按相关检验操作规程对产品进行检验,合格后填写成品检验报告,车间统计凭质量授权人审批的《成品检验放行审核表》办理入库手续。
4.3 产品生产过程中的技术控制
4.3.1新产品正常投产生产前,生产工程部按照工艺部编制工艺验证
方案实施验证,确定工艺的可行性,并做记录。
4.3.2生产过程中的特殊工序和关键工序必须编制相应的标准操作规
程,验证其工艺的可行性和安全性。设置必要的工序质量控制点,实施连续的监视和控制,并作好记录。其它工序可视实际需要而定
4.3.3生产过程使用的标签、合格证、使用说明书、小包装应有专人
保管,其领用、发放、使用、销毁应有记录。
4.4 特殊工序和关键工序的控制
4.4.1 公司特殊工序指:焊接、喷涂、酸洗。
公司关键工序指:整机测试工序。
4.4.2新产品初次生产时,研发部应制定特殊工序及关键工序,并组织对其进行初次验证。
4.4.3 已经转为量产的产品,特殊工序和关键工序发生变更时,工艺部应对其进行验证。
4.4.4特殊过程的确认按《验证和确认控制程序》执行。
4.4.5设置必要的工序质量控制点,实施连续的监视和控制。
4.5车间退料
4.5.1车间领出的多余物料需要退回仓库的由班组长开具《请验单》写明产品名称、数量、规格型号及入库原因交检验员检验,检验员检验合格的物料开具检验单标明车间物料退回仓库,交仓库保管员。4.5.2 检验员检验出不合格品的,生产车间,质量部,采购,研发进行评审后进行处理。
4.5.3 如入库前材料已经进行评审的,退库时按照评审的标准进行退料处理。
4.5.4 处理的方式有再加工,报废,退货等。
4.5.5 仓库对退库后材料根据最后确定的处理方式进行重新统计,如因报废,退货等造成材料紧缺的,应通知采购及时购买。
4.5.6车间加工过程中产生的废料由操作者将其退回原来料库,由原材料保管进行称重、存放,因料废产生的费用按《质量成本管理制度》执行。
4.6研发样机生产