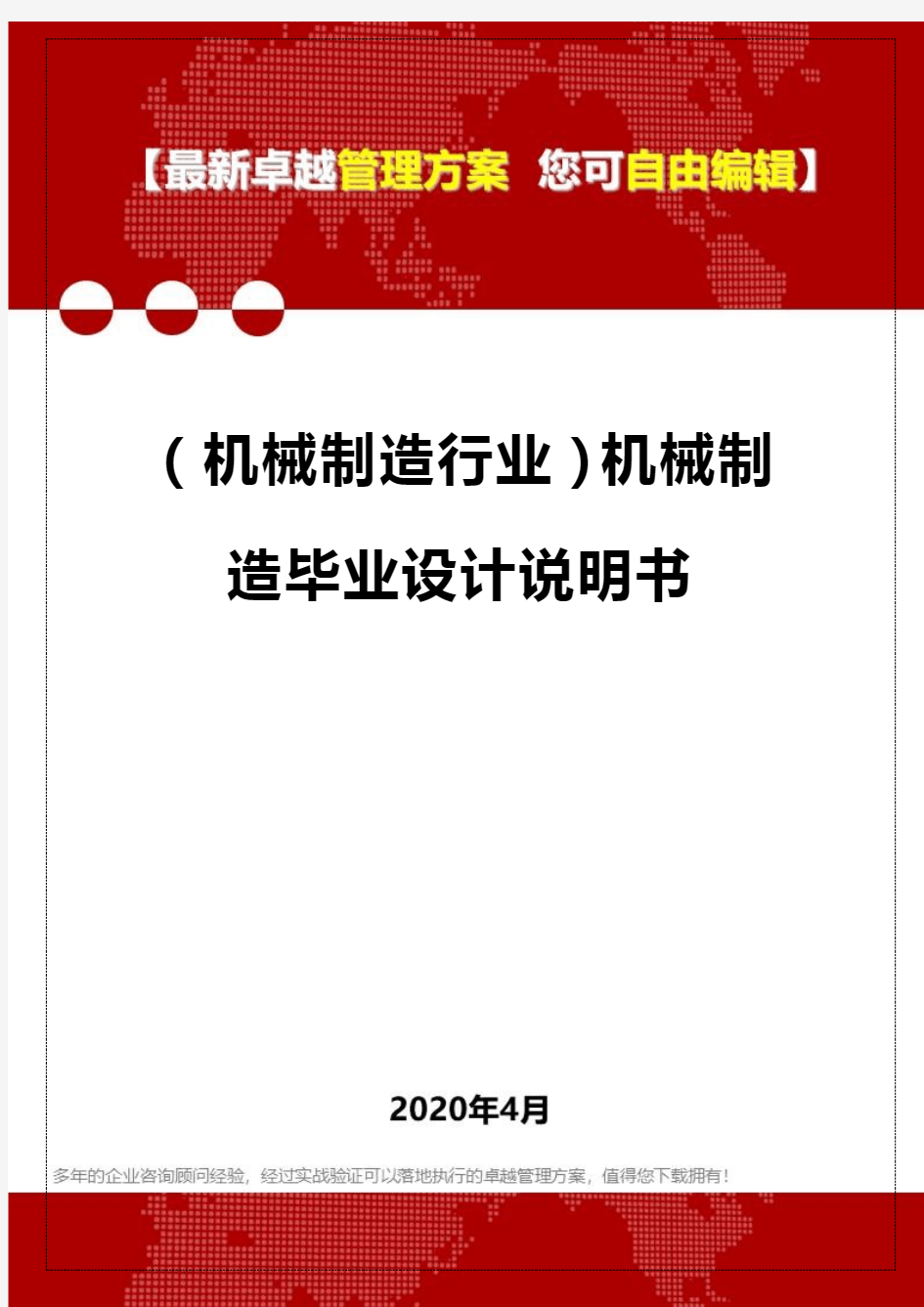
(机械制造行业)机械制造毕业设计说明书
- 格式:doc
- 大小:4.21 MB
- 文档页数:41
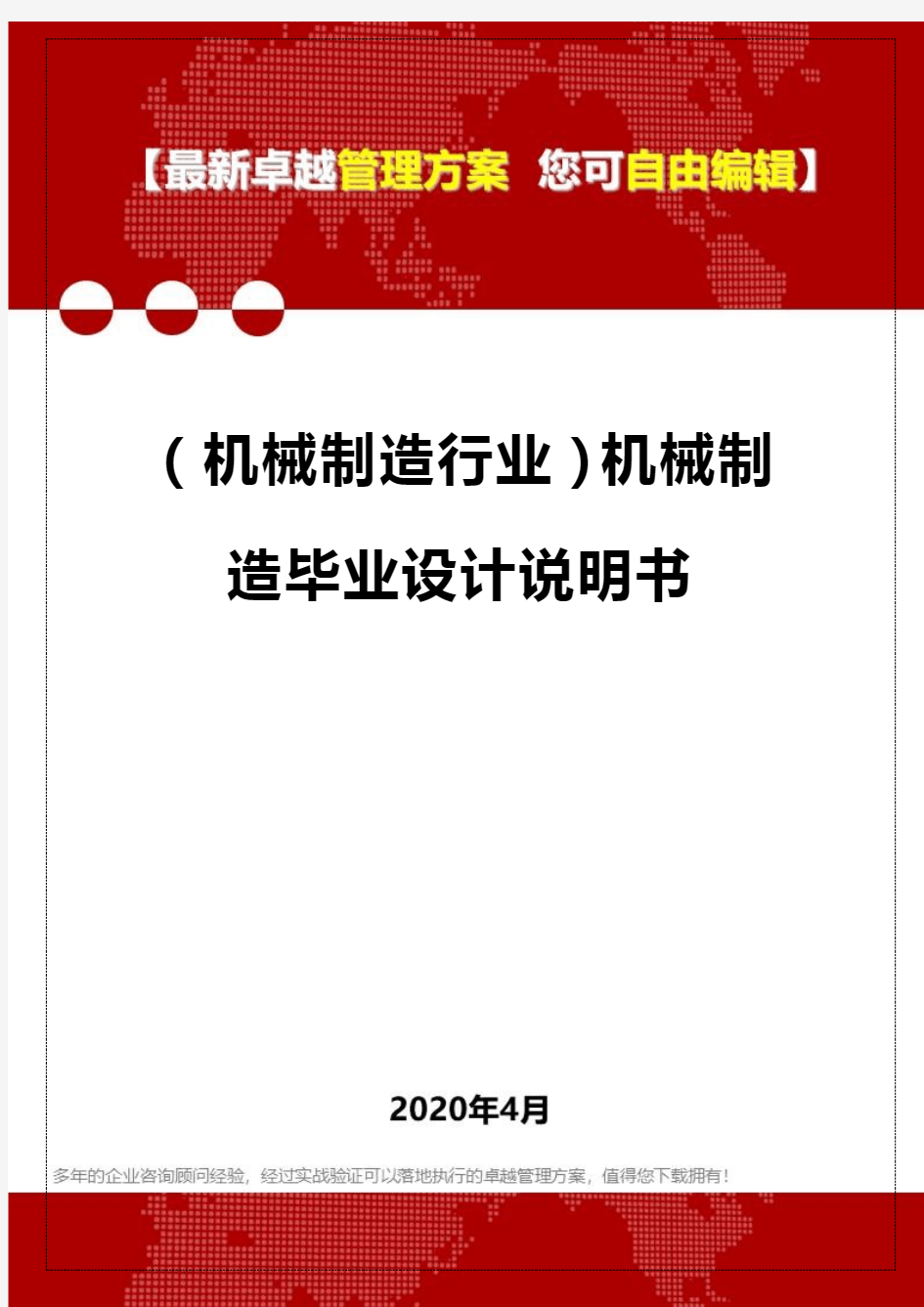
(机械制造行业)机械制造毕业设计说明书
目录
一、任务内容 (4)
二、任务技术要求 (4)
三、汇总相关专业知识点 (4)
1.数控铣削加工特点 (4)
2.确定加工路线时应遵守以下原则 (5)
3.尺寸精度的影响因素 (5)
4.形位精度的影响因素 (5)
5.薄壁零件铣削 (6)
6.零件几何尺寸的处理方法 (6)
7.刀具半径补偿修调 (7)
8.顺铣与逆铣的选择 (7)
9.切削用量的确定 (8)
10.精加工余量的确定 (9)
11.确定刀具切入切出路线 (10)
12.任意角度倒角和倒圆 (10)
13.确定最短加工路线 (11)
14.合理选用切削液 (13)
15.机用虎钳的找正及安装 (13)
16.试切对刀·14
四、端盖零件加工工艺,程序编制及加工 (16)
1.设备及工具选用 (16)
2.零件图纸分析 (18)
3.零件的加工工艺分析 (19)
4.零件的装夹方案确定 (19)
5.零件加工所用刀具及切削用量选用 (20)
6.工件原点及零件几何要素确定 (21)
7.制定数控加工工艺卡片及刀具卡片 (22)
8.走刀路线图 (23)
9.数控加工程序编制 (24)
10.试切加工及注意事项 (27)
结束语 (29)
致谢 (29)
参考文献 (29)
一、任务内容
试用数控完成如图1-1所示工件的编程与加工。
要求:零件的各加工技术要求符合图纸要求。
图1-1零件图纸
绘制零件图形三维效果图
二、任务技术要求
技术要求如下:
(1)以年产量5万件生产;
(2)不准用砂布及锉刀等修饰表面;
(3)加工精度及表面质量符合图纸要求;
注:(1)毛坯材料:硬铝;
(2)毛坯尺寸:100×100×30。
三、汇总相关专业知识点
1.数控铣削加工特点
①对零件加工的适应性强、灵话性好,能加工轮廓形状特别复杂或难以控制尺寸的零件,
如模具类、壳体类零件等。
②能加工普通机床无法加工或很难加工的零件,如用数学模型描述的复杂曲线类零件以及三维空间曲面类零件。
③能加工一次装夹定位后,需进行多道工序加工的零件。如可对零件进行钻、扩、镗、铰、攻螺纹、铣端面、挖槽等多道工序的
加工。
④加工精度高,加工质量稳定可靠。
⑤生产自动化程度高,生产效率高。
⑥从切削原理上讲,端铣和周铣都属于断续切削方式,不像车削那样连续切削,因此对刀具的要求较高,刀具应具有良好的抗冲击性、韧性和耐磨性。在干式切削状况下,还要求刀具具有良好的红硬性。
2.确定加工路线时应遵守以下原则
①确定加工路线应能保证零件的加工精度和表面粗糙度要求,并保证高的加工效率。
②为提高生产效率,在确定加工路线时,应使加工路线最短,刀具空行程时间最少。
③所确定的加工路线应当能够减少编程工作量,以及编程时数值计算的工作量。
在使用以上原则的时候,还应当考虑零件的加工余量,机床的加工能力等问题。
3.尺寸精度的影响因素
铣削加工过程中产生尺寸精度降低的原因是多方面的,在实际
素的条件要充分,应无引起矛盾的多余尺寸或者影响工序安排的封闭尺寸等。例如,如图1-2所示,由于零件轮廓各处尺寸公差带不同,那么,用同一把铣刀、同一个刀具半径补偿值编程加工时,就很难同时保证各处尺寸在尺寸公差范围内。这时要对其尺寸公差带进行调整,一般采取的方法是:在保证零件极限尺寸不变的前提下,在编程计算时,改变轮廓尺寸并移动公差带,如图1-2所示的括号内的尺寸,编程时按调整后的基本尺寸进行,这样,在精加工时用同一把刀,采用相同的刀补值,如工艺系统稳定又不存在其他系统误差,则可以保证加工工件的实际尺寸分布中心与公差带中心重合,保证加工精度。
图1-2零件尺寸公差带的调整图1-3刀具半径补偿
7.刀具半径补偿修调
刀具半径补偿除方便编程外,还可灵活运用,实现利用同一程序进行粗、精加工,即:
粗加工刀具半径补偿=刀具半径+精加工余量
精加工刀具半径补偿=刀具半径+修正量
刀具半径补偿如图1-3所示,刀具直径为ф20立铣刀,现零件粗加工后给精加工留余量单边1.0㎜,则粗加工刀具半径补偿D01的值为:
㎜
粗加工后实测L尺寸为L+1.98,则精加工刀具半径补偿D11
值应为:
㎜
则加工后工件实际L值为L-0.03。
8.顺铣与逆铣的选择
如图1-4所示,根据刀具的旋转方向和工件的进给方向间的相互关系,数控铣削分为顺铣和逆铣两种。在刀具正转的情况下,刀具的切削速度方向与工件的移动方向相同,采用左刀补铣削为顺铣;刀具的切削速度方向与工件的移动方向相反,而采用右刀补铣削为逆铣。
采用顺铣时,其切削力及切削变形小,但容易产生崩刃现象。因此,通常采用顺铣的加工方法进行精加工。而采用逆铣则可以提高加工效率,但由于逆铣切削力大,导致切削变形增加、刀具磨损加快。因此,通常在粗加工时采用逆铣的加工方法。
图1-4顺铣与逆铣
9.切削用量的确定
数控编程时,编程人员必须确定每道工序的切削用量,并以指
令的形式写入程序中。对于不同的加工方法,需要选用不同的切削
用量。切削用量的选择原则是:保证零件加工精度和表面粗糙度,充分发挥刀具切削性能,保证合理的刀具耐用度;并充分发挥机床的性能,最大限度提高生产率,降低成本。总之,切削用量的具体数值应根据机床性能、相关的手册并结合实际经验用类比方法确定。同时,使主轴转速、切削深度及进给速度三者能相互适应,以形成最佳切削用量。
(1)切削用量计算:
已知:直径Ф60,齿数4,取每齿吃刀量fz=0.06㎜/r,f=4×0.06=0.24㎜/r,设切削速度V=80m/min
主轴转速n=1000V/πD
=1000×80/3.14×60
=424r/min
进给量F=f·S
=0.24×424
=101.76㎜/min
(2)我们在取切削用量时,可以适当变化一些,要根据加工时的实际情况来调整。当加工精度,表面粗糙度要求高时,进给速度应选小些,转速较高一点。刀具空行程时,特别是远距离“回零”时,