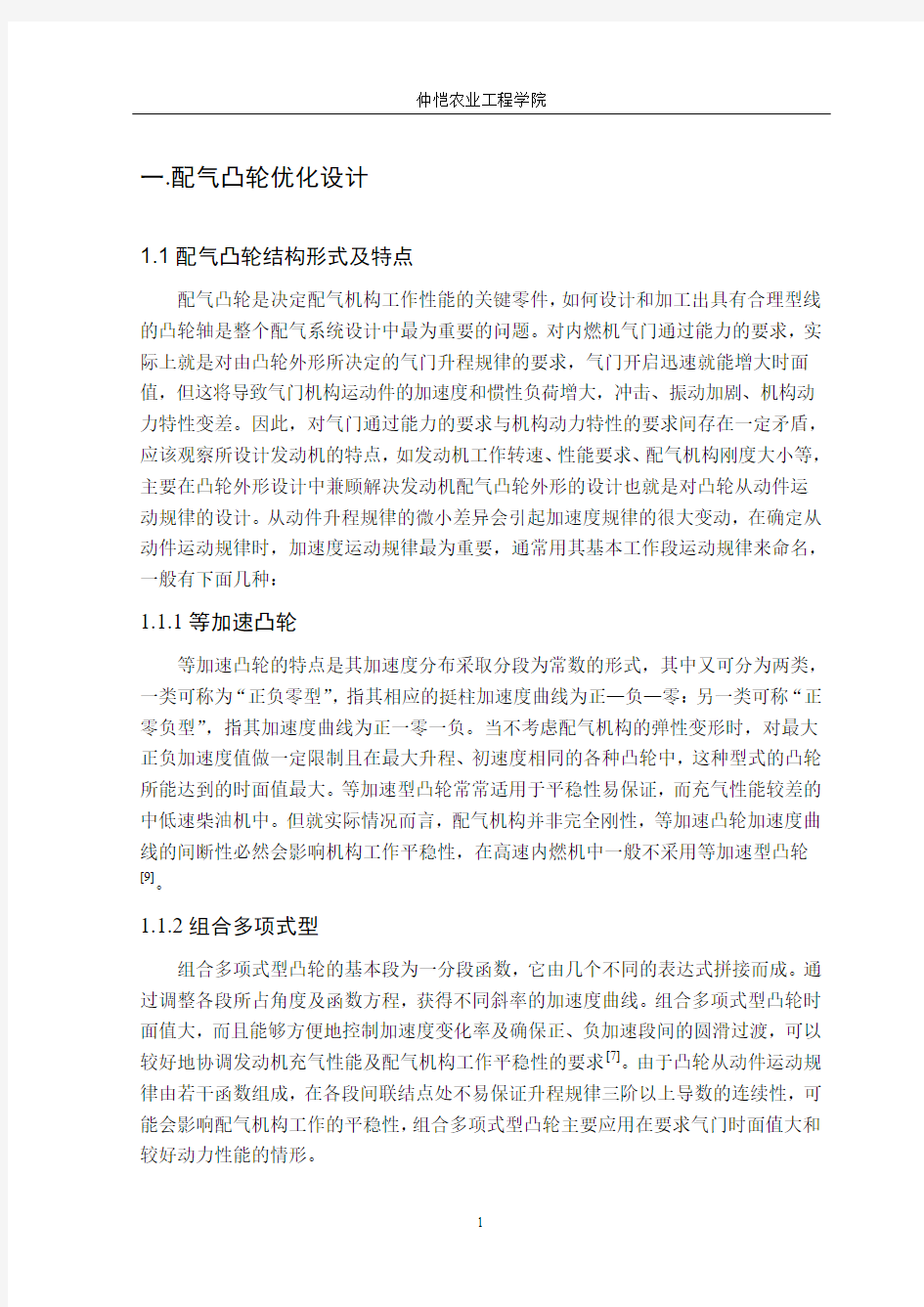
凸轮优化设计
- 格式:doc
- 大小:522.09 KB
- 文档页数:18
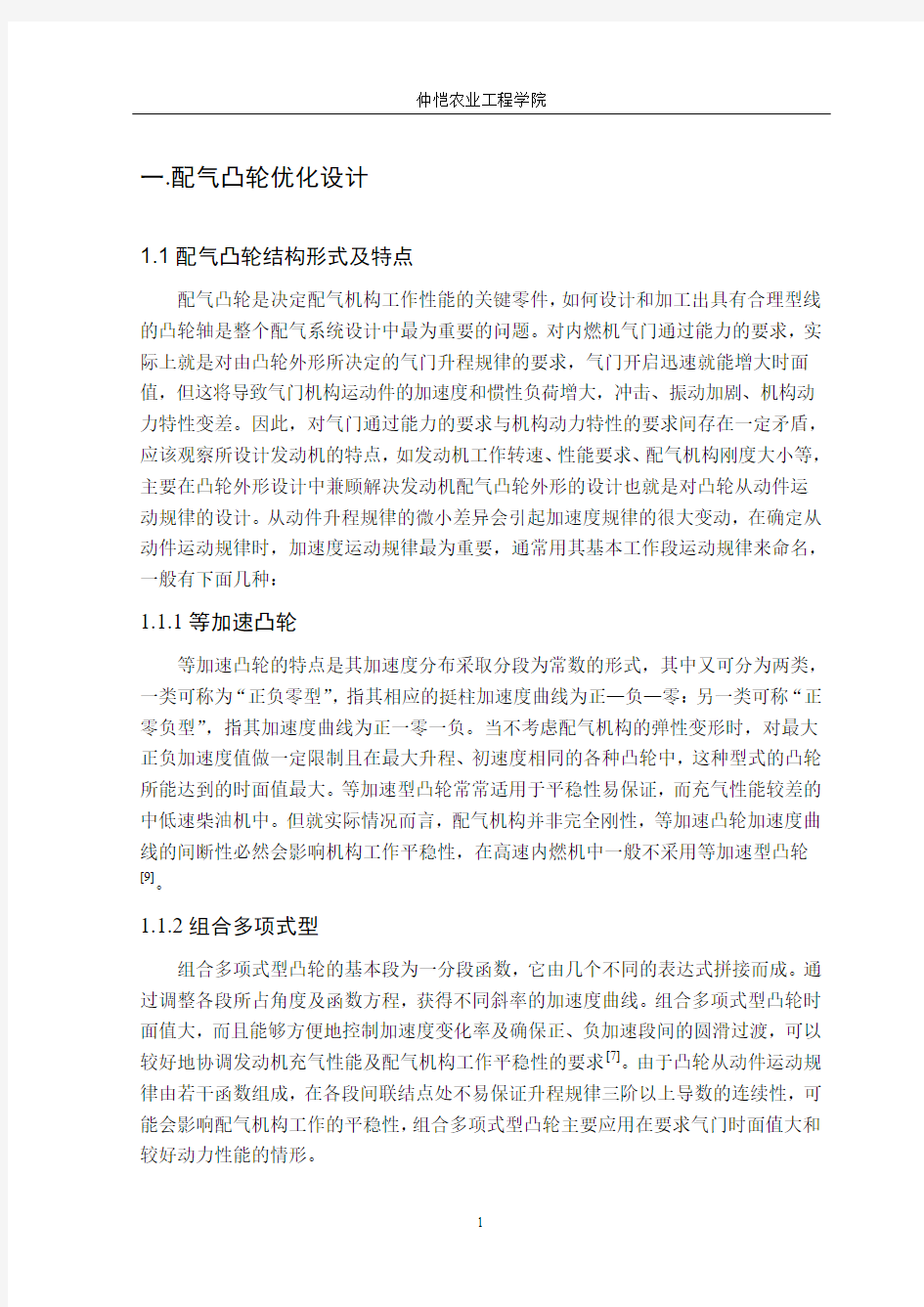
一.配气凸轮优化设计
1.1配气凸轮结构形式及特点
配气凸轮是决定配气机构工作性能的关键零件,如何设计和加工出具有合理型线的凸轮轴是整个配气系统设计中最为重要的问题。对内燃机气门通过能力的要求,实际上就是对由凸轮外形所决定的气门升程规律的要求,气门开启迅速就能增大时面值,但这将导致气门机构运动件的加速度和惯性负荷增大,冲击、振动加剧、机构动力特性变差。因此,对气门通过能力的要求与机构动力特性的要求间存在一定矛盾,应该观察所设计发动机的特点,如发动机工作转速、性能要求、配气机构刚度大小等,主要在凸轮外形设计中兼顾解决发动机配气凸轮外形的设计也就是对凸轮从动件运动规律的设计。从动件升程规律的微小差异会引起加速度规律的很大变动,在确定从动件运动规律时,加速度运动规律最为重要,通常用其基本工作段运动规律来命名,一般有下面几种:
1.1.1等加速凸轮
等加速凸轮的特点是其加速度分布采取分段为常数的形式,其中又可分为两类,一类可称为“正负零型”,指其相应的挺柱加速度曲线为正—负—零:另一类可称“正零负型”,指其加速度曲线为正一零一负。当不考虑配气机构的弹性变形时,对最大正负加速度值做一定限制且在最大升程、初速度相同的各种凸轮中,这种型式的凸轮所能达到的时面值最大。等加速型凸轮常常适用于平稳性易保证,而充气性能较差的中低速柴油机中。但就实际情况而言,配气机构并非完全刚性,等加速凸轮加速度曲线的间断性必然会影响机构工作平稳性,在高速内燃机中一般不采用等加速型凸轮[9]。
1.1.2组合多项式型
组合多项式型凸轮的基本段为一分段函数,它由几个不同的表达式拼接而成。通过调整各段所占角度及函数方程,获得不同斜率的加速度曲线。组合多项式型凸轮时面值大,而且能够方便地控制加速度变化率及确保正、负加速段间的圆滑过渡,可以较好地协调发动机充气性能及配气机构工作平稳性的要求[7]。由于凸轮从动件运动规律由若干函数组成,在各段间联结点处不易保证升程规律三阶以上导数的连续性,可能会影响配气机构工作的平稳性,组合多项式型凸轮主要应用在要求气门时面值大和较好动力性能的情形。
1.1.3高次方凸轮
高次方凸轮是目前整体式的函数凸轮型线中应用较为广泛的一种。它的基本段挺柱升程函数是高次多项式,项数和幂次的选取有一定的任意性。一般情况下,幂指数越大,升程曲线就越丰满,且最大负加速度越小,而使凸轮外形最小曲率半径增大,有利于减小该处接触应力、降低磨损。但是其负加速度初段形状不理想,往往会提高对弹簧的要求,而且还使最大正加速度值增大,正加速度段宽度减小,导致配气机构振动加剧。在设计过程中,一般先针对若干组幕指数,计算出反映凸轮特性的各相关参数,确定性能较好的一组作为计算方案。高次多项式型凸轮主要应用在对动力性能要求较高的现代高速车用发动机上[22]。
1.1.4多项动力凸轮
以上三种型线的凸轮都是把配气机构视为完全刚性的。但配气机构总是存在弹性变形。无论挺柱升程怎样设计,它与气门升程之间总是有差别的,因此,基于这一差别的考虑,对挺柱升程曲线预先做一定的修正,这样使用动力学计算方法算出的气门升程曲线才比较理想。多项动力凸轮基本工作段的气门升程曲线是高次多项式来设计的,因此能够进行这种动力学修正的型线有很多种,应用最为广泛的是多项动力凸轮,这种凸轮具有良好的高速适应性。目前多项动力凸轮主要应用在高速汽油机中。1.2配气凸轮优化设计方法
内燃机配气凸轮优化设计的优劣直接影响到其动力性、经济性、可靠性、振动、噪声与排放特性的好坏。配气凸轮的丰满系数越大,则进气量越多,内燃机的动力性能与经济性能越好,排气烟度与热负荷越低,凸轮形线的圆滑性越好,内燃机的振动与噪声越小;凸轮与挺柱间的接触应力越小;润滑特性越好,内燃机配气机构的冲击载荷及摩擦磨损越小。
配气凸轮型线优化设计的任务就是在确保配气机构能可靠工作的前提下寻求最佳的凸轮设计参数。凸轮型线的设计己从静态设计、动态设计发展到系统动力学优化设计,系统动力学设计考虑配气机构的弹性变形,可更精确地描述配气机构的运动和受力情况,并统一考虑机构动态参数与凸轮型线,从而实现凸轮型线优化设计。1.2.1静态优化设计
在静态优化设计中,将配气机构看成绝对刚体。不考虑它在运动时的弹性变形。用此方法设计凸轮型线主要用三项指标来判别其好坏。
1)静态充气性能。通常用挺柱升程丰满系数和时面值来表示,希望此值越大越好。
2)静态加油度峰值。即挺柱最大正加速度a
max 和最大负加速度a
min
,也就是说a
max
和a
min
的绝对值越小,高速动态性能越好。
3)凸轮廊面最小曲率半径,或者凸轮与挺柱表面的接触应力。设计凸轮时,应避免其最小曲率半径过小,这样会导致接触应力很大,并会使凸轮过早磨损。一般认为最小曲率半径应大于2mm。
用静态优化设计法设计的圆弧凸轮,虽然加速度曲钱不连续,配气机构惯性力有突变,但有较大时面值。对转速不高的发动机来说,它所引起的振动和噪声较小,故在较低转速的发动机上还有一定的使用价值。但随着发动机转速的提高,振动和噪声趋向严重。为解决此问题,人们又用此法设计了函数凸轮,如复合正弦凸轮及复合摆线凸轮等。这类凸轮型线变化形式较多,但其加速度曲线都是连续的。当内燃机转速进一步提高时。配气机构的弹性变形引起气门强烈振动,严重时会破坏气门的正常工作,产生飞脱和反跳,这不仅加剧了发动机的振动、噪声和各零件间的磨损,还会使充气性能有所下降,为了解决这些问题,人们就提出了动态设计的方法[14]。
1.2.2动态优化设计
在动态优化设计中,考虑弹性变形。把配气机构看成弹性系统,主要由下列指标来评价凸轮型线。
1)气门的动态加速度峰值。也就是根据单质量振动模型或多质点振动模型计算出的最大正加速度波蜂值和第一个负加速度波谷值的大小,以及落座后的气门动态响应。
2)动态充气性能。即考虑进排气管压力波动,多缸机各缸的抢气现象,配气相位对充气性能的影响。随着内燃机转速的提高,静态和动态充气性能的差别越来越大,这主要是由两部分因素引起的,一是当转速提高。吸气过程缩短,进排气管压力波的动态效应增大;另一方面气门发生飞脱和反跳,破坏了正常的静态充气性能。
3)挺柱与凸轮表面的动力润滑磨损情况以及气门头部的磨损情况。但在实际上这些指标受到一些限制,如在动态充气性能计算中必须考虑到进排气管中的压力波动情况、配气相位的影响,这就需要求解一元不等熵流动的特征线方程组,而精确求解该方程组比较困难。另外动态充气性能主要受到进排气管和气道的结构尺寸的影响,所以往往把它和凸轮型线分开计算。凸轮脚面与挺柱表面的动力润滑一般只用道森半经验公式进行计算,所以有时也不考虑,实际上所谓的动态优化设计只比静态优化设计多考虑了动态加速度峰值,一般将配气机构简化成单质点振动模型。用振动模型的动态加速度正负峰值来判断凸轮型线的好坏。
用动态优化设计方法设计的凸轮有多项动力凸轮、正弦抛物线凸轮、rL次谐波凸轮等。多项动力凸轮只从弹性变形的角度出发设计凸轮外形,并未考虑配气机构的