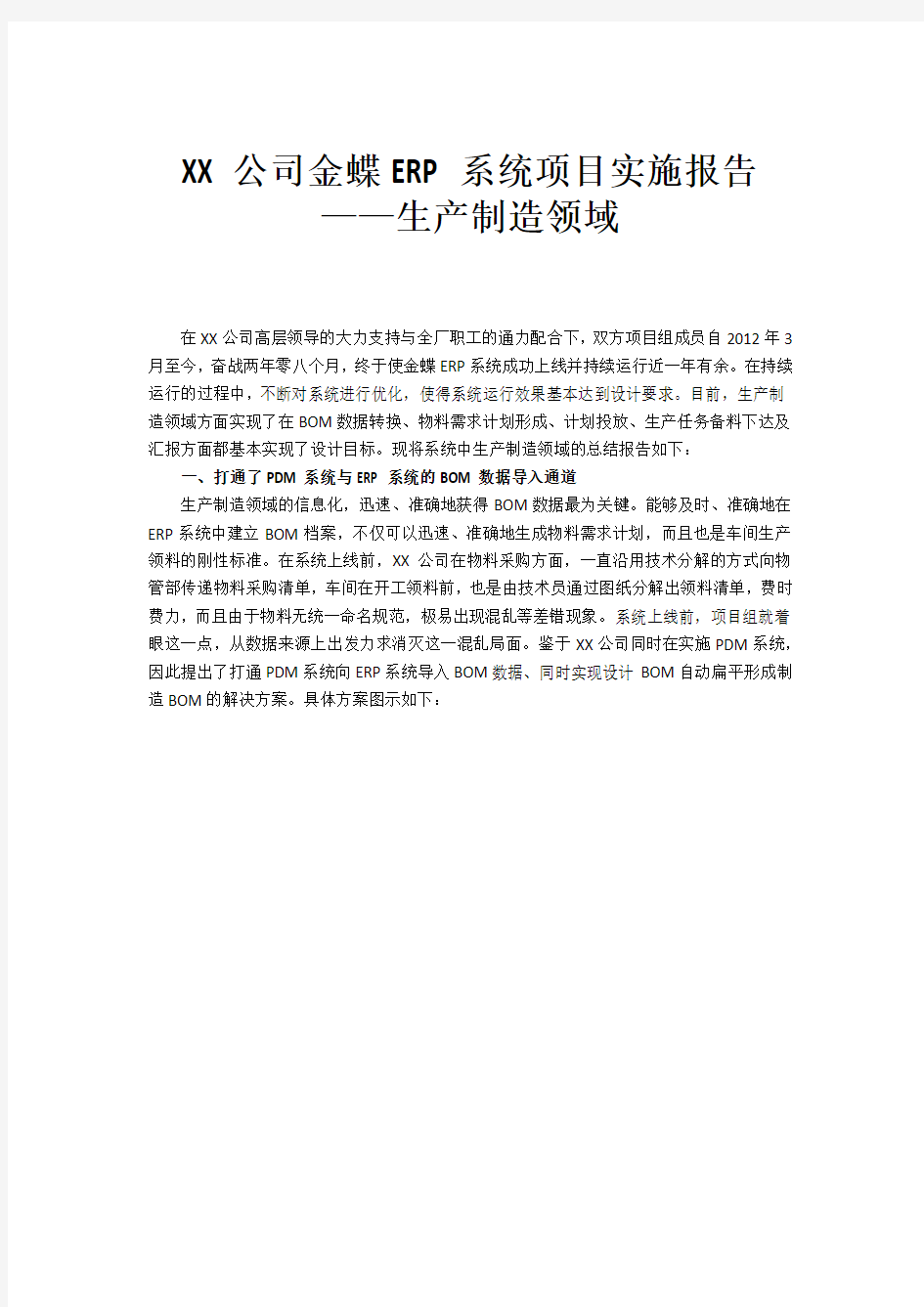
XX公司金蝶ERP系统项目实施报告
- 格式:docx
- 大小:5.47 MB
- 文档页数:23
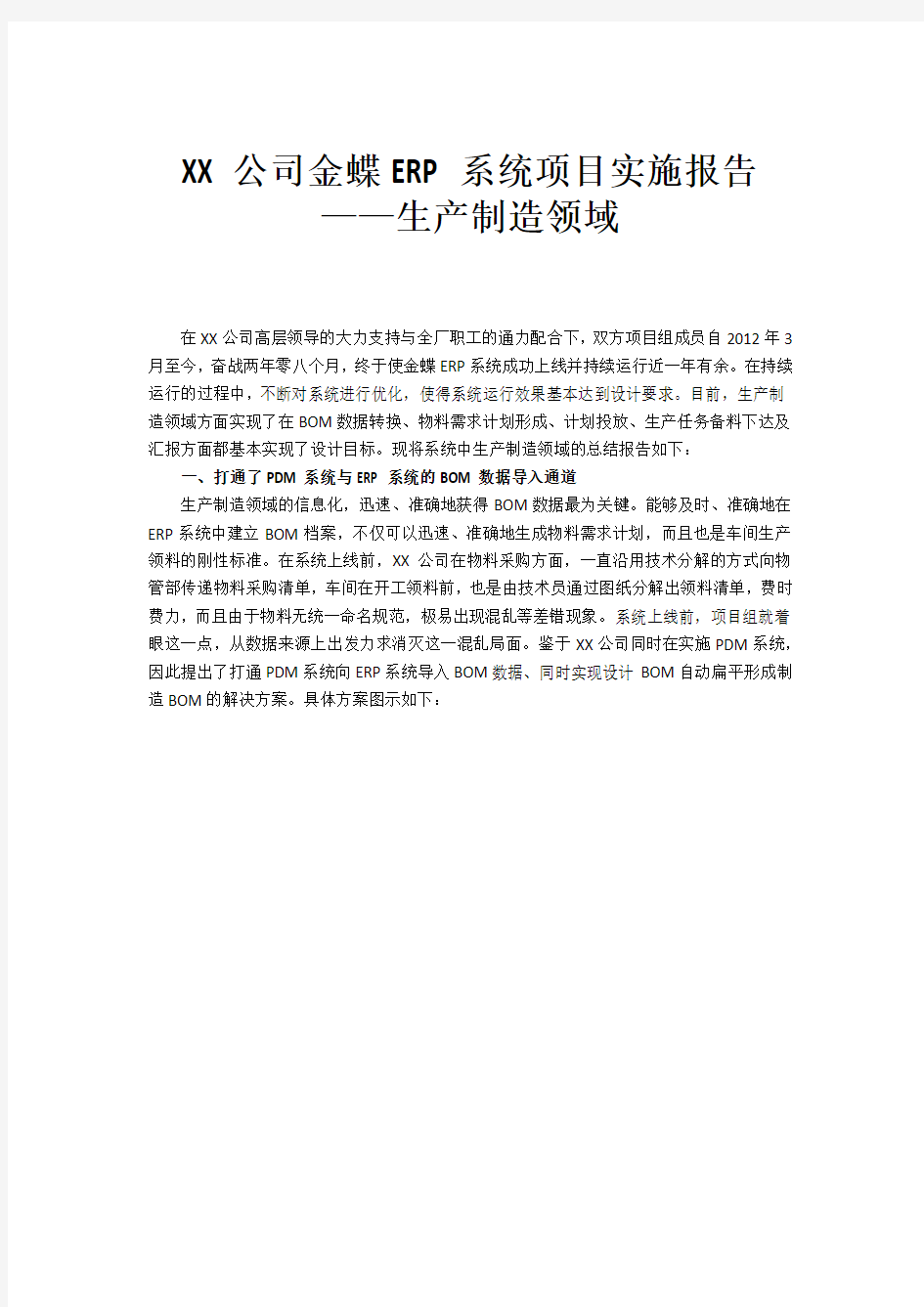
XX公司金蝶ERP系统项目实施报告
——生产制造领域
在XX公司高层领导的大力支持与全厂职工的通力配合下,双方项目组成员自2012年3月至今,奋战两年零八个月,终于使金蝶ERP系统成功上线并持续运行近一年有余。在持续运行的过程中,不断对系统进行优化,使得系统运行效果基本达到设计要求。目前,生产制造领域方面实现了在BOM数据转换、物料需求计划形成、计划投放、生产任务备料下达及汇报方面都基本实现了设计目标。现将系统中生产制造领域的总结报告如下:
一、打通了PDM系统与ERP系统的BOM数据导入通道
生产制造领域的信息化,迅速、准确地获得BOM数据最为关键。能够及时、准确地在ERP系统中建立BOM档案,不仅可以迅速、准确地生成物料需求计划,而且也是车间生产领料的刚性标准。在系统上线前,XX公司在物料采购方面,一直沿用技术分解的方式向物管部传递物料采购清单,车间在开工领料前,也是由技术员通过图纸分解出领料清单,费时费力,而且由于物料无统一命名规范,极易出现混乱等差错现象。系统上线前,项目组就着眼这一点,从数据来源上出发力求消灭这一混乱局面。鉴于XX公司同时在实施PDM系统,因此提出了打通PDM系统向ERP系统导入BOM数据、同时实现设计BOM自动扁平形成制造BOM的解决方案。具体方案图示如下:
见以下截图,可以具体深入了解CAXA PDM系统中设计BOM转换到ERP系统中制造BOM 的过程。
注:为了保密,以下截图均对物料描述进行了删除
1.图1.1 :CAXA PDM系统中的设计BOM(设计人员预先对BOM节点进行了扁平化
标识)
图1.1 某产品设计BOM结构(局部)
2.图1.2:向中间表写入数据
图1.2 向中间表写入数据
3.图1.3:ERP系统读取中间表,并进行对物料编码、工号等要素的合法性校验
图1.3 ERP系统读入中间表时进行合法性检查
4.图1.4:ERP系统中制造BOM导入成功(导入过程中根据物料制造策略自动判断是
否引用蓝图的节点,若ERP系统中蓝图BOM已存在,则不重复导入)
图1.4 制造BOM导入成功
目前,PDM-ERP的BOM导入接口程序已趋于完善,应用部门使用效果良好。由于BOM 数据的存在,无需技术人员再根据设计图纸分解物料清单,从而提高了工作效率。
二、建立起以销售订单为主要需求来源的主生产计划、物料需求计划体系
库存积压与供料不及时、人工编制生产计划准确性不高、计划执行不易跟踪等现象是长期困扰制造型企业的管理难题,XX公司也不例外。系统上线之前,生产制造部每月10日左
右负责将销售部门新签的销售订单信息以生产大计划的方式下达给设计、物管、车间等相关部门,由于销售订单交期变更频繁、产品设计周期不易控制等种种原因,致使生产部无法准确考虑交期变更、设计延误等因素,从而制定考虑产能制约因素影响的产品制造计划,而只能以上述所谓大计划的方式下达给相关部门,而这个大计划,实际上就是客户订单列表(记录了产品型号、订货数量、交期以及最新承诺交期等因素)。在技术准备(修改单下达)与物料准备到位的情况下,车间就可以在大计划范围内选择其中准备到位的计划执行开工。当然,生产部会在当月末发布下月的必保计划,作为物管、生产等部门采购、生产的最后依据。但是可以看出,必保计划发布明显太迟,无论是供应部门还是生产单位都明显无法按照迟来的必保计划作为生产前期准备的依据。这样的计划管理模式会一是导致计划部门无法控制对计划的投放、对生产进度的控制,二是无法指导物料采购采购计划的进行,事实上形成了一旦设计修改单下达,供应部门便自行采购,而各车间去向物管部门要料的奇怪现象,这进而又造成了生产延误的现象频出。
工欲善其事,必先利其器,ERP系统的核心MPS/MRP就是为解决这一困局而准备的。ERP生产制造系统上线后,重新梳理相关流程,主要改进措施如下:
1.要求市场部与业务同步,随时维护销售订单,作为需求来源随时通过系统传递给计划部门,一改以往固定在每月10日集中提供销售订单信息的模式;同时要求市场部将最终确认的交期通过变更处理体现在销售订单上;
2.生产制造部以销售订单作为需求来源形成需求计划,通过MPS/MRP运算形成产品制造计划,产品制造计划应考虑交期变更、设计周期、产能等因素的影响进行人工修正(主要是计划开始、完成日期),同时可以将无销售订单的其他需求(如售后服务投产计划、补投计划、产品试制计划等)补充到产品制造计划,并确认审核后,再次进行MRP计算形成物料采购计划。
3.增加计划投放环节。计划投放能够对计划执行进行有效管控,只有将计划投放下去才能进行相应的物料采购与生产开工,从而加强了计划部门对计划执行的控制力度,一改以往供应部门与生产部门依据设计完成后(即修改单下达)即可擅自进行采购与生产开工的混乱局面。
4.作为独立组织的高压分公司,由本部投放生产计划(投放成跨组织的调拨订单),生产计划到达该组织后,进行MPS/MRP运算,产生产品制造计划与物料采购计划,因其无采购权,物料采购计划委托本部物管部门采购,到货后由该组织收货。产品生产完工后,再调拨回本部。
如此,便形成了以修正过的产品制造计划拉式生成物料采购计划的计划管理模式,从而避免了此前生产计划对采购业务缺乏指导性、对生产进度缺乏控制的困顿局面,进而实现产销平衡、供给及时、减少不合理库存占用的目标。
当前,基于ERP系统的计划管理模式运行流程如下图所示:
以下截图展示基于ERP系统的计划管理模式的实现成果:1.图2.1 以销售订单为需求来源的需求计划列表:
图2.1 需求计划列表
2.图2.2 MPS/MRP运算
图2.2 MPS/MRP运算
3.图2.3 计划订单生成
图2.3 计划订单生成
4.计划订单投放
计划订单
采购申请单
图2.4.1 外购件计划订单投放成采购申请单